65Mn high-carbon spring steel is a material that is quite versatile and is used for many purposes due to its exceptional strength, toughness, and elasticity. In this guide, we will provide an exhaustive explanation of 65Mn steel, focusing on its key properties, common applications, and its advantages across a wide range of domains. Be you a materials expert, an engineer, or someone who is simply inquisitive about this remarkable alloy, this blog post will come in handy. This article intends to explain how 65Mn high-carbon spring steel is unique, where it is most utilized, and why it is so widely chosen for engineering and industrial applications.
What is 65Mn Carbon Steel?
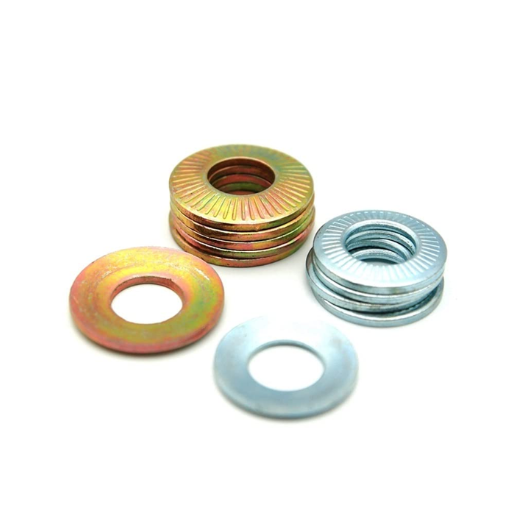
65Mn high-carbon steel is a high-carbon alloy containing manganese. It is known for its exceptional toughness and wear resistance, along with its ability to withstand considerable load-bearing stress. Its composition features about 0.9-1.2%(weight) carbon and 0.9-1.2%(weight) manganese, being widely accepted for its hardness and elasticity after undergoing heat treatment. This also makes it the preferred option for components such as springs, knives, and other robust, enduring tools needing durable deformation-resistant materials.
Understanding the Composition of 65Mn Steel
65Mn steel is an alloy with exceptional traits like strength and flexibility is rightfully denoted as a high-performance alloy. The properties of this steel give it a competitive edge over modern alloys, making it a prized possession. Mechanically, it possesses the capacity for enduring tremendous stress and resisting elastically or through structural deformation. Additionally, 65Mn steel exhibits enduring shapes under abrasive practices while withstanding extreme conditions. These features further enable this steel to help create durable tools like springs and knives capable of enduring tough performance requirements. It also possesses remarkable characteristics for reshaping and forming under adversarial conditions, making it irreplaceable.
How Does 65Mn Compare to Other Carbon Steels?
65Mn steel is far more distinguishable than other alloys owing to it being carbon steel, as it possesses an uncanny blend of elasticity, toughness, and hardness. 65Mn contains greater amounts of manganese as compared to standard carbon steels (0.9-1.2%), thus making it more desirable in terms of strength and hardness. Furthermore, having high components of carbon (0.9-1.2%) makes this alloy special amongst general-purpose steels since it is meant for wear resistant and damage-hospitable applications. 65Mn will not only outperform medium carbon steels under heavy stress, it will also outperform them in fatigue resistance and deformation under heat treatment. Thus, 65Mn is being increasingly preferred while formulating advanced performance components like springs and cutting knives because other alloys provide unreliable and less precise outcomes.
Applications of 65Mn Spring Steel
The 65Mn spring steel is highly used in cases where there is a need for high durability, high elasticity, and high resistance against wear. It’s mostly used for the manufacturing of different types of springs like automotive suspension springs, industrial machinery springs and precision mechanical components. Due to its hardness and edge retention after being subjected to proper heat treatment, it is also used for manufacturing blades, cutting tools, and agricultural implements.
Key Technical Properties:
- Tensile Strength: 980-1180 MPa (after heat treatment).
- Hardness: 48-55 HRC (after quenching and tempering).
- Elastic Limit: Excellent range of resilience and recoverable range.
- Wear Resistance: High, suitable for abrasive materials.
- Machinability: Moderate, concerning appropriate techniques that can achieve intended results.
These characteristics enable 65Mn steel to withstand wear and make it a preferred choice in applications which require components that must not wear under great stress, cyclic loads or high monotonic load.
What Makes 65Mn Steel Stand Out?
The 65Mn steel grade is remarkable for having high levels of hardness, toughness, and wear resistance simultaneously. Such materials which are able to carry great amounts of stress while remaining elastic under repetitive loading are ideal for highly demanding applications. Also, considering its moderately low machinability, it is able to be crafted accurately, which makes it versatile for various industrial uses. In addition, 65Mn steel is easy to work with when turned to the desired shape of a component and thus used for industrial crafters.
Exploring the Mechanical Properties of 65Mn
According to my analysis, 65Mn steel has highly favorable mechanical properties such as high tensile strength, great strength, and superb wear resistance. Its balance of toughness and durability is optimal for materials that experience heavy loads along with repetitive stress like in springs and cutting tools. The steel performs well when put through various treatments, especially those that increase elasticity and resistance to deformation, leading to higher performance. These traits make 65Mn a reliable and versatile material for a range of industrial tasks.
The Role of Manganese in 65Mn Steel
The importance of manganese in improving the properties of 65Mn steel is paramount. It enhances the steels hardeness, wear resistance, tensile strength, and shock or heavy load absorption capability. Moreover, manganese improves the overall quality of steel by acting as a deoxidizer and eliminating impurities during the steelmaking process. Additionally, it further aids in resisting deformation and improves the steels toughness.
Technical Terms Relevant to Manganese in 65Mn Steel:
- Manganese Concentration: Normally ranges from 0.90% – 1.20%
- Ultimate Tensile Strength: Nearly 1230 MPa (when subjected to suitable heat treatment)
- Ultimate Elastic Modulus: Approximately 200 GPa
- Hardness: Reaches 50-60 HRC post-quenching and tempering
With the right composition of manganese, 65Mn steel gains the necessary strength and durability, therefore becoming a commonly used material in several challenging operations.
Why Choose 65Mn for Cutting Tools?
An alloy steel grade 65Mn is ideal for use in cutting tools because it combines strength, elasticity, and durability extremely well. Its high manganese content adds to its impact resistance as well as its ability to hold an edge under stress. 65Mn has high hardness levels after heat treatment (50-60 HRC), which provides the ability to cut tough materials. Also, its modulus of elasticity permits efficient springback, which is important for precision in demanding cutting applications. When compared to other tool steels, 65Mn is a relatively inexpensive yet durable tool steel for saw blades, chisels, and knives, which ensures service life and reliability.
How is 65Mn Carbon Steel Used in Knife Making?
65Mn carbon steel has gained tremendous popularity as a knife forging material owing to its toughness and edge retention while still being very economical. Due to the high manganese content, the blade can be made thin and sharp yet extremely durable. Knives manufactured from 65Mn grade steel are suited to heavy-duty tasks like cutting, chopping, and carving because the steel is impact resistant. The ease with which the knife can be sharpened adds to its practicality for professional use or daily use.
Benefits of Using 65Mn Steel for Blades
Based on my experience, 65 Mn steel is the best steel due to its durability and performance for blades. The high carbon content allows it to retain an edge and endure many demanding tasks such as chopping and carving. Even more, the steel’s manganese composition boosts its hardness and resistance to wear, further increasing its usefulness in heavy-duty applications. In my experience, 65Mn steel is relatively easy to sharpen, which makes the maintenance of blade sharpness convenient. Therefore, 65Mn steel provides dependable utility for professionals and casual users.
Heat Treatment Process for 65Mn Knives
The 65Mn knife’s heat treatment process is one of the most important processes that determines the balance between its hardness, toughness, and wear resistance. Below are some of the steps with their respective parameters:
- Annealing – The steel is to be heated to 680 -750 degree Celsius and to be kept there between 2 to 4 hours. This step helps in softening the steel, alleviating its internal stresses, and also improves its machinability.
- Hardening – The steel has to be heated to between 850 degree celsius to 880 degree celsius until it reaches a uniform temperature. Locking it in oil or water after quick quenching helps in preserving its hardness and wear resistance.
- Tempering – This step reduces the brittleness and enhances the toughness of the steel. The knife has to re reheated to between 200 to 300 degrees Celsius and must be held for 1 to 2 hours. The Air cooling must follow this step. The exact tempering temperature will depend on the intended application and desired hardness.
If these steps are followed diligently, the knife is optimally prepped for heavy duty while cyclically ensuring ease of maintenance.
Comparing 65Mn and 1095 Steel for Knives
The analysis of 65Mn and 1095 steel shows marked differences in composition, properties, and performance, which makes both of them suitable for their particular application. Here is a summary of the key differences:
- Composition:
- 65Mn Steel: This is a Chinese alloy manganese steel with a carbon and manganese composition of around 0.62%-0.70% and 0.90%-1.20%, respectively. Manganese addition improves toughness and wear resistance, and moderate carbon content supports good edge retention.
- 1095 Steel: An American high carbon steel, 1095 has approximately 0.90%-1.03% carbon which increases its hardness and edge retention. It does not have considerable alloying elements which makes the steel simpler and easy to sharpen.
- Hardness (HRC):
- 65Mn Steel: This steel typically hardens to around 55-58 HRC. This value provides good durability and chipping resistance while maintaining decent sharpness.
- 1095 Steel: Can reach hardness levels of 56-60 HRC, depending on the heat treatment done. The higher potential HRC means better edge retention, particularly for fine cutting tasks.
- Toughness:
- 65Mn Steel has superior toughness due to its manganese content. It is good for use in machetes and survival knives, or any application that sustains impact and repeated stress.
- 1095 Steel has relatively lower toughness and hence is more likely to chip under heavy use or impact, making this better suited for slicing or cutting applications.
- Corrosion Resistance:
- Both steel are not classified as stainless due to insufficient chromium content. However, 65Mn resists corrosion slightly better than 1095 due to manganese’s positive impact on surface corrosion stability. Regular care is needed for both to eliminate rust.
- Ease of Sharpening:
- Due to limited tools in the field, 65Mn is more suited for use in the field as the steel is easy to sharpen.
- 1095 Steel is more difficult to sharpen than 65Mn, but retains a keen edge for a longer period, which has benefits for fine detail work.
- Applications:
- 65Mn Steel finds its applications in large, heavy-duty knives, such as machetes, axes, and other outdoor tools. Toughness and durability are very important in these cases.
- 1095 Steel is better suited for small fixed blades or EDC knives that benefit from sharpness and high-level detail work.
Summary of Technical Parameters:
Property | 65Mn Steel | 1095 Steel |
---|---|---|
Carbon Content | 0.62%-0.70% | 0.90%-1.03% |
Manganese Content | 0.90%-1.20% | None |
Typical Hardness (HRC) | 55-58 | 56-60 |
Corrosion Resistance | Low (better than 1095) | Low |
Toughness | High | Moderate |
Edge Retention | Moderate | High |
Ease of Sharpening | Easy | Moderate |
Primary Use | Heavy-duty cutting | Precision cutting |
When choosing between 65Mn and 1095 steel, consider the intended purpose of the knife, as well as factors like edge retention, toughness, and maintenance requirements. Both steels serve their roles effectively when applied correctly.
What are the Chemical and Physical Properties of 65Mn Steel?
65Mn steel’s composition includes 0.6-0.7% carbon alongside 0.9-1.2% manganese. The manganese and carbon content increases durability and strength since it can attain higher hardness with the application of heat treatment.” 65Mn also has traces of silicon, phosphorus, and sulfur, making the alloy even more workable and robust.
Primarily, 65Mn steel is renowned for its great resistance to wear and high tensile strength, which allows the use of the alloy in demanding environments. Additionally, it possesses good elasticity, which accounts for the phenomenon of enduring high-impact repetitive stress. These properties make 65Mn a great steel for springs, machetes, and cutting blades. On the downside, the alloy is more susceptible to corrosion compared to stainless steel and therefore requires frequent upkeep.
Analyzing the Chemical Composition of 65Mn
The chemical composition of 65Mn steel is carefully balanced to provide its specific mechanical properties. Its primary components are carbon (C) at roughly 0.62-0.70% , which adds to its high tensile strength and abrasion resistance, as well as Manganese (Mn), in the range of 0.90-1.20%, which enhances wear resistance, toughness, and hardenability. The small amount of silicon (Si) at about 0.17-0.37% improves elasticity and overall strength. Trace amounts of phosphorus (P) and sulfur (S) are kept under 0.035% so as not to compromise the steel’s structure.
This specific composition gives the desired mechanical properties of toughness and resilience under repeated stress, making it ideal for use in springs, saw blades, and agricultural tools. The chemical structure allows for excellent quenching properties with a typical range of 55-62 HRC post heat treatment, depending on the method used. It is important to note that the lower chromium content limits the corrosion resistance of the steel, meaning it requires proper care and maintenance to reduce rusting over time.
Physical Characteristics: Hardness and Toughness
The toughness and hardness of 65Mn steel make it suitable for specific demanding applications. With adequate heat treatment, 65Mn attains a hardness level of 55-62 HRC, which is excellent for tasks that require resistance to wear. Additionally, the content of manganese improves the toughness of the material, enabling it to bear considerable impact or stress without breaking. This, in turn, aids in achieving optimal balance in properties for scenarios like spring manufacturing or cutting tools. Maintaining a delicate balance in heat treatment and tempering is important to maintain ductility, as too much toughness at high loads can introduce brittleness.
Corrosion Resistance and Durability Factors
From my understanding of corrosion resistance, it is said to be mainly dependent on the material combination, along with the environment. For example, there is a lack of inherent ability to resist corrosion for high-carbon steels. This is because they are not treated, covered, or alloyed with compounds like chromium, which strengthen them in moist or acidic conditions. The ability to withstand mechanical forces over time or in constantly changing environmental factors links heavily to the material’s durability. Harsh environments can have their impacts lessened significantly with maintenance such as protective coatings or control of other elements.
Is 65Mn Carbon Steel Right for Your Project?
Keeping in mind the primary features and application specifics of 65Mn carbon steel helps in determining its suitability for a project. This high-strength, high-carbon steel is esteemed for its outstanding wear resistance, toughness, and edge retention, making it perfect for tools, blades, and springs. However, its limited resistance to corrosion means that it may need protective coatings or regular maintenance in humid or corrosive environments. If your project seeks above-average performance under stress and is on a budget, then 65Mn could prove to be a fitting material. Yes, that’s right: you were just offered value along with reliability. Now, perform a final check to see if the 65Mn carbon’s parameters align with your requirements.
Evaluating the Pros and Cons of 65Mn
After going through the primary materials, here is the assessment of the 65 carbon manganese steel:
Advantages
- High Endurance Limit – 65Mn has a marked tensile strength value, making it favorable for use in springs and cutting tools.
- Good Resistance – Due to its carbon and manganese content, 65Mn also has remarkable resistance to wear.
- Economically Priced – Unlike other high performing steel, the strength and durability of 65Mn due not come at a steep price.
Disadvantages
- Low Corrosion Resistance – The lack of protection is a major issue in humid and corrosive environments.
- Brittle at High Hardness – Thin or small cross-sections tend to fail catastrophically due to impact, and heating provides lots of strength but also some brittleness.
Regular Maintenance Required – In order to extend its life, machinery oil or other protective substances must be applied.
In conclusion, 65Mn manganese and carbon steel are strong contenders for most carbon steel instruments, but they require frequent maintenance to reduce the risk of corrosion.
Comparing 65Mn with Other High-Carbon Steels
This is where my balance comparison of forged 65Mn and other high-carbon steels begins. Out of all of them, I would argue that 65Mn is the most versatile due to its combination of hardness and wear resistance. While being on the more affordable end, it does outperform competing high-carbon steels like 1095, which focuses solely on edge retention, or tool steel D2, which specializes in toughness. On the downside, the steel will rust without the right care, furthering its reputation as a high-carbon steel. Nonetheless, I stand by 65Mn for more demanding uses like springs and cutting tools, assuming a lack of need for corrosion resistance doesn’t pose an issue.
Factors to Consider When Choosing the Best Steel
To determine what type of steel best suits your needs, keep the following in mind:
- Hardness
- The Rockwell scale (HRC) is used to measure this value.
- Sharper steels offer better edge retention and wear resistance (D2 tool steel provides 58-62 HRC) but may have reduced toughness.
- Toughness
- Toughness is the measure of a steel’s ability to resist breaking upon impact.
- An affordable option is 65Mn steel, providing a good balance between toughness and strength, ideal for springs.
- Corrosion Resistance
- Stainless steels like 440C or 420 show great performance in moist and chemically active environments.
- High carbon steels such as 65Mn require maintenance to avoid rust.
- Workability and Sharpening
- Sharpening and working with softer steels (1055 or 5160) is easier, but they dull quicker.
- D2 tool steel is harder to sharpen due to its high hardness, yet that makes it more durable.
- Cost
- Since premium applications require high-end steel, CPM S35VN and M390 are offered at higher prices.
- Performing well at a reasonable price is 65Mn or 1095.
After reviewing these parameters along with your specifications, you can select your best option for the to achieve the right mix of performance, longevity, and cost effectiveness.
References
- SteelPro Group – 65Mn High Carbon Spring Steel: This source provides detailed information on the properties, uses, and characteristics of 65Mn steel.
- Corten Steels – 65Mn Spring Steel: This page discusses the hardness, tempering, and annealing properties of 65Mn steel.
- Lee Knives – 65Mn Carbon Steel: This article explains the toughness, composition, and advantages of 65Mn steel, especially in knife-making.
Frequently Asked Questions (FAQ)
Q: What is the 65Mn composition and its significance in high-carbon spring steel?
A: The 65Mn composition includes a carbon content of 0.62-0.70%, manganese ranging from 0.90-1.20%, and other elements like silicon, phosphorus, and chromium. This composition makes it a high-strength and wear-resistant alloy, suitable for applications requiring good elasticity and resilience.
Q: How does the carbon content in 65Mn affect its properties?
A: The higher carbon content in 65Mn, typically between 0.62-0.70%, contributes to its high hardness and wear resistance. This amount of carbon is ideal for providing edge retention and toughness, making it suitable for tools like steel knives and machetes.
Q: What are the main advantages of using 65Mn high-carbon spring steel?
A: 65Mn offers excellent wear resistance, good toughness, and high hardness. It is wear-resistant and provides good elasticity, making it ideal for use in steel products and applications such as automotive components and machinery parts.
Q: How does 65Mn compare to plain carbon steel and stainless steel?
A: Compared to plain carbon steel, 65Mn has better wear resistance and edge retention due to its higher carbon and manganese content. Unlike stainless steel, which contains chromium for corrosion resistance, 65Mn focuses on toughness and strength, which makes it more suitable for applications like swords and tools requiring high stress tolerance.
Q: What is the typical use of 65Mn in the production of steel knives and other tools?
A: 65Mn is often used to make steel knives, machetes, and swords due to its high hardness, good toughness, and excellent edge retention. These properties are essential for cutting tools that require durability and sharpness over extended periods.
Q: Is 65Mn brittle, and how does it handle stress?
A: While 65Mn is high-strength and offers good toughness, it can become brittle if improperly heat-treated. However, when correctly processed, it maintains good elasticity and resilience, making it suitable for high-stress applications in the automotive and machinery industries.
Q: How does the elasticity of 65Mn benefit its applications?
A: The good elasticity of 65Mn allows it to return to its original shape after being deformed, making it ideal for applications such as springs and automotive components where flexibility and resilience are crucial.
Q: What are the common challenges when working with 65Mn high carbon steel?
A: Challenges include managing its brittleness if not heat-treated properly and ensuring the correct balance of alloying elements for desired properties. Proper processing is essential to maintain its high hardness and wear resistance.
Q: Can 65Mn be used interchangeably with 1065 tool steel?
A: While both 65Mn and 1065 are high-carbon steels and share similar properties, 65Mn typically offers better wear resistance and toughness due to its manganese content. However, specific applications may dictate the choice based on desired properties such as elasticity and hardness.
Q: Why is 65Mn sometimes referred to as Chinese spring steel?
A: 65Mn is often referred to as Chinese spring steel because it is widely produced and used in China for making springs and other resilient components. Its composition and properties make it particularly suited for applications requiring high tensile strength and good elasticity.