High-strength, low-alloy steels are transforming industries that require durability, economy, and versatility in their applications. The HX420LAD coil is one of the few HSLA materials for manufacturers that want to maintain the delicate balance between strength and formability. From the automobile industry to developments and heavy machinery, understanding the specific properties and advantages of the HX420LAD could help transform a project. This blog explores the properties of HX420LAD coils and their applications, as well as the key benefits that businesses need to produce top-grade and sustainable products. Read along to know what helps this great material find its way into modern-day engineering.
Introduction to HSLA HX420LAD Coil
High-strength low-alloy (HSLA) HX420LAD coil is a specialized steel product for extraordinary strength, durability, and flexibility. Higher yield strength and better formability are the primary hallmarks of this precious metal, which serves industries that require both performance and precision. The HX420LAD will undoubtedly enhance corrosion resistance and find suitable applications in automotive fabrication, construction, and other heavy-duty industrial settings where reliability is a key consideration under all circumstances. Thus, it is best suited among lightweight and sustainable designs that cannot jeopardize structural integrity.
What is HSLA HX420LAD?
HSLA HX420LAD, being a high-strength and low-alloy steel, is developed for the utmost levels of durability, formability, and corrosion resistance. It is extensively used in automotive and structural applications for lightweight and high-performance designs.
Overview of EN 10346 Standard
EN 10346 primarily covers requirements and technical delivery standards for continuously hot-dip coated steel products. Coatings can consist of zinc, aluminum-zinc, or even a layer of zinc-aluminum-magnesium-alloy, which is widely regarded as the best since it offers the utmost corrosion resistance and durability. In maintaining the highest regard for competing standards, EN 10346 is widely used by automotive companies, construction firms, and appliance manufacturers to ensure the quality and uniform performance of coated steel products.
According to EN 10346, this specification encompasses a broad range of grades, each with distinct mechanical properties and protective requirements. For instance, HX420LAD grades are recognized as the highest strength and very formable grades used in lightweight and sustainable design. The mechanical properties of these materials, including their minimum yield strength, tensile strength, and percentages of elongation, are established not only for their intended application but also for specific defined uses.
Under EN 10346, datasheets define essential parameters:
- Thickness Range: The thickness range is generally considered to be between 0.35 m and 3.0 mm, concerning the product.
- Coating Mass: The total coating mass is expressed in grams per square meter (g/m²) and may vary with the type of coating applied. Take Z275, for instance: this coating refers to a zinc coating with a total of 275 g/m² on both sides.
- Mechanical Properties:
- Yield Strength (Re): This parameter varies from one grade to another, and the values typically lie between 140 MPa and 550 MPa.
- Tensile Strength (Rm): This is usually denoted within a level of 270 MPa to 700 MPa.
- Elongation (A80): It is expressed as a percentage, ranging from 18% to 34%, depending on the grade and application.
The EN 10346 standard demonstrates a strong commitment to sustainability by promoting the use of recyclable materials and advanced coating technologies that can extend the product’s service life.
This far-reaching and thoroughly detailed standard guarantees steel solutions of a certain quality, which modern engineering and construction projects demand.
Importance of High-Strength Low-Alloy Steels
Key Point | Details |
---|---|
High Strength-to-Weight Ratio | Lighter than carbon steel, maintains high strength. |
Improved Corrosion Resistance | Alloying elements enhance resistance to rust and environmental degradation. |
Enhanced Weldability | Maintains good weldability for diverse applications. |
Improved Formability | Can be bent and shaped without cracking. |
Cost-Effective | Reduces material and fabrication costs. |
Applications in Construction | Used in bridges, buildings, and structural beams. |
Automotive Benefits | Improves fuel efficiency and safety in vehicles. |
Pipeline Durability | Ideal for oil, gas, and water pipelines in harsh environments. |
Heavy Equipment Use | Suitable for machinery under high stress. |
Energy Efficiency | Reduces weight, improving energy and fuel efficiency. |
Mechanical Properties of HSLA HX420LAD Coil
HSLA HX420LAD coils offer intriguing mechanical properties applicable in demanding applications. This material has a minimum yield strength of 420 MPa, ensuring adequate structural integrity under stress. The tensile strength ranges from 480 to 620 MPa, allowing for high loads to be imposed without undergoing plastic deformation. It also offers good elongation values, which are pertinent to its flexibility and formability. In light of these properties, HSLA HX420LAD coils are used within the automotive, construction, and engineering sectors whenever strength and durability are required.
Yield Strength and Other Mechanical Properties
The HSLA HX420LAD coils are designed to meet rigorous mechanical requirements with enhanced qualities of strength, durability, and flexibility. Some of the fundamental mechanical properties of this material include:
- Yield Strength: 420 MPa (minimum), ensuring permanent deformation under stress and thereby providing structural integrity.
- Tensile Strength: 480-620 MPa provides excellent resistance to permanent deformation when subjected to large loads.
- Elongation at Break: About 18-20%, which allows for good formability, lateral bending, or pneumatic shaping operations.
- Elastic Modulus: Approximately 210 GPa, this value is due to the material’s stiffness resisting any potential elastic deformation.
- Density: About 7.85 g/cm³, which contributes to a weight that is robust but manageable.
The mechanical properties of HX420LAD make HSLA coils an ideal material for critical industries that demand a perfect balance of strength and flexibility.
Ladle Analysis for Quality Assurance
Ladle analysis is conducted to ensure the quality and consistency of HSLA HX420LAD coils. It primarily involves specific chemical composition tests at the ladle stage of steelmaking to verify adherence to desired specifications. Below are five key packaged elements that are checked for:
- Carbon: Usually kept at a maximum of 0.12 to maintain strength without affecting weldability.
- Manganese typically ranges from 1.2 to 1.6, and it enhances both tensile strength and toughness.
- Silicon: Has to be kept at a maximum of 0.5 to increase hardness and resist oxidation.
- Phosphorus: Has to be kept at a maximum of 0.025 to prevent the steel from being brittle against ductility.
- Sulfur must be kept at a maximum of 0.015 to prevent inclusion and enhance machinability.
These material specifications ensure the properties of these steels, making them suitable for demanding industrial applications.
Surface Quality Considerations
Ensuring a surface with precise quality would be the foremost consideration in meeting high-performance requirements in industrial applications. Surface defects, such as scratches, pitting, or unevenness, would severely compromise the functionality of materials, rendering them resistant to fatigue and durable only for a short while. They must be detected and prevented using various advanced defect detection methods, such as ultrasonic testing (UT) and eddy current testing (ECT).
Recent industrial studies reveal that the permitted roughness average (Ra) in critical applications, such as automotive and aerospace components, typically lies in the range of 0.2 to 1.5 micrometers, depending on the specific application. For example, bearing surfaces with an Ra value of less than 0.4 microns are preferred for improved wear resistance and a longer service life. Such precision levels are made possible by precision machining processes, such as CNC grinding and polishing.
Eventually, improvements in surface quality are achieved through surface treatments such as shot peening, electroplating, or chemical passivation. These treatments enhance corrosion resistance and bring aesthetic and functional improvements to the material. Adopting a holistic approach toward surface quality management ensures compliance with strict industry standards and yields improved reliability of the products in various applications.
Chemical Composition of HSLA HX420LAD Steel
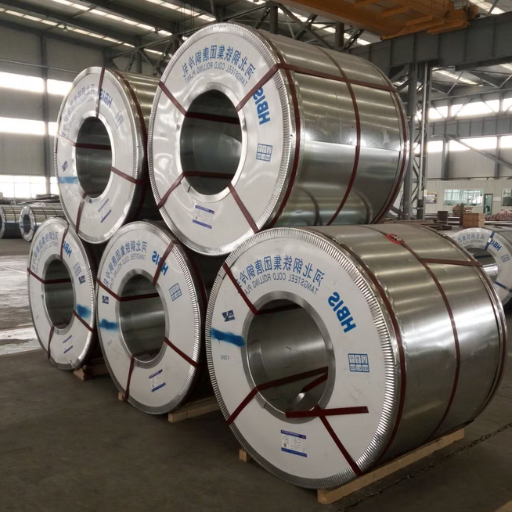
The composition of HSLA HX420LAD steel is arranged to enable high strength and good formability. Common elements in this steel include:
- Carbon (C): up to 0.12% max
- Silicon (Si): up to 0.50% max
- Manganese (Mn): up to 1.60% max
- Phosphorus (P): up to 0.025% max
- Sulfur (S): up to 0.015% max
- Aluminum (Al): greater than or equal to 0.015% (for deoxidation)
- Niobium (Nb), Titanium (Ti), and Vanadium (V) are added in trace amounts for strengthening.
Their composition ensures high strength, weldability, good fatigue resistance, and corrosion resistance, making HX420LAD steel suitable for highly demanding structural and automotive applications.
Key Elements in Chemical Composition
- Carbon (C): Typically ≤ 0.10%
Carbon plays a crucial role in determining the strength and hardness of HX420LAD. Lower amounts of carbon improve weldability and formability, which is critical for automotive and structural applications.
- Manganese (Mn): ≤ 1.60%
Manganese enhances the tensile strength and wear resistance of steels. Furthermore, it deoxidizes the steels by removing unwanted oxygen during the steelmaking process. Balanced amounts of manganese ensure the steel does not become brittle at the expense of ductility.
- Phosphorus (P): ≤ 0.025%
Strict control over phosphorus content is essential since higher content would increase embrittlement, especially at low temperatures. Lower phosphorus levels, therefore, result in improved steel life.
- Sulfur (S): ≤ 0.015%
Sulfur content is controlled to maintain machinability without imparting poor impact resistance. Too much sulfur can cause the formation of undesirable brittle phases in steel.
- Aluminum (Al): ≥ 0.015%
Aluminum acts as a deoxidizer to remove oxygen dissolved in molten steel, yielding a clean and sound material. This also assists grain refinement, which benefits strength and toughness.
- Niobium (Nb), Titanium (Ti), and Vanadium (V): Trace amounts
These microalloying elements enhance the strength of HX420LAD by precipitating fine carbides or nitrides, thereby contributing to grain refinement and improving toughness and fatigue resistance.
- Silicon (Si): Typical addition ≤ 0.50%
Silicon enhances hardness and strength, acting as an excellent deoxidizer. It also helps the steel resist corrosion and oxidation, especially in high-temperature processing.
- Chromium (Cr): Trace amounts, typically ≤ 0.25%
Chromium enhances corrosion resistance and provides some secondary hardening, allowing HX420LAD to perform well in demanding environments.
- Boron (B): ≤ 0.005%
The addition of trace boron enhances hardenability, particularly in thin sections, and ensures uniform strength and toughness across various component geometries.
Summary
By maintaining a strict balance of these elements, HX420LAD steel achieves a high strength-to-weight ratio, excellent weldability, and superior fatigue and corrosion resistance. The composition of the alloy is designed to meet the current engineering needs for lightweight, tough, and safe materials in structural and automotive applications.
Comparison with Other Steel Types
Parameter | HSLA HX420LAD | Carbon Steel | Dual Phase (DP) Steel | Martensitic Steel |
---|---|---|---|---|
Strength-to-Weight Ratio | High | Moderate | High | Very High |
Yield Strength (MPa) | ~420 | ~250 | ~330-700 | ~900-1700 |
Tensile Strength (MPa) | ~480 | ~400-550 | ~490-1000 | ~900-2000 |
Formability | Good | Excellent | Moderate | Low |
Weldability | Excellent | Excellent | Good | Moderate |
Corrosion Resistance | Improved | Low | Moderate | Low |
Applications | Automotive, construction | General-purpose | Automotive, structural parts | Safety-critical automotive |
Cost | Moderate | Low | Moderate | High |
Steel Equivalent Grades
Comparisons can be made between HX420LAD and several other high-strength, low-alloy steel grades used worldwide. These equivalent grades are somewhat alike in mechanical properties and applications and hence may be considered substitutes in several engineering situations. Hereunder is a list of five commonly used equivalent grades with their designations and standards:
- S420MC (EN 10149-2)
- Thermomechanically rolled steel of European grade, S420MC, exhibits high strength and excellent weldability; therefore, it is commonly used in automotive and structural applications.
- HSLA Grade 50 (A1011/A1018 ASTM)
- American-grade HSLA steel with similar tensile strength and formability, and mainly used for lightweight construction and transport.
- QStE420TM (DIN EN10149-2)
- German-grade steel is characterized by high yield strength and enhanced toughness, making it ideal for cold forming.
- JSC440W (JIS G3113)
- Japanese-grade HSLA steel, realized as the automotive industry’s best-grade formability and surface quality.
- SAPH440 (JIS G3134)
- A high-strength steel grade from Japan for structural and automotive use, with a good balance of formability and strength.
The equivalencies demonstrate HX420LAD steel’s global versatility and adaptability in meeting diverse industrial standards.
Coating and Surface Treatment Options
Coating and surface treatment options for HX420LAD steel are crucial for achieving higher corrosion resistance and durability, particularly in heavy-duty applications. Typical options include:
- Zinc Coating (Galvanization): The zinc coating provides excellent corrosion protection by creating a barrier and a scratch layer.
- Aluminum-Silicon Coating: Protects against corrosion and heat, particularly in high-temperature environments.
- Organic Coatings (Paints): Good for aesthetics, but also add extra protection against exposure to the elements.
- Phosphating: Prepares the surface for painting or coating by creating a uniform, adhesive layer.
These processes prepare the steel to meet performance-based and longevity requirements across varied applications.
Hot Dipped Galvanized vs. Other Coatings
Parameter | Hot Dipped Galvanized | Zinc Plating | Powder Coating | Epoxy Coating |
---|---|---|---|---|
Application Process | Immersion in molten zinc | Electrochemical plating | Electrostatic powder spray | Sprayed liquid epoxy |
Coating Thickness | 2-8 mils | 0.2-0.5 mils | Variable, typically thicker | Thin film |
Corrosion Resistance | High, self-healing properties | Moderate | High, barrier protection | Moderate |
Durability | Long-lasting, 75+ years | Shorter lifespan | Durable, UV-resistant | Prone to cracking |
Environmental Impact | Environmentally friendly | Chemical-intensive | Eco-friendly, low emissions | Chemical-intensive |
Color Options | Limited (silver-gray) | Limited (silver) | Wide variety | Multiple options |
Cost | Moderate | Low | Moderate | Moderate to high |
Best Applications | Outdoor, structural steel | Indoor, light-duty items | Decorative, indoor/outdoor | Small residential projects |
Importance of Zinc Coating in Automotive Applications
Zinc coating is crucial in the realm of autos chiefly because it prevents the corrosion of steel components, renders durability to an item, and consequently cuts maintenance costs. Zinc-coated steel is heavily relied upon by automotive manufacturers to satisfy the safety, performance, and environmental standards. Below are the five main advantages of zinc coating for automotive applications:
- Corrosion Protection: Zinc acts as a sacrificial coating for steel, preventing rust and thereby increasing the lifespan of automotive components, even in the harshest environments, such as winter roads treated with salt.
- Increased Durability: With the improved resistance to the action of moisture and road grit, zinc-coated steel renders vehicles more resilient and reliable with time.
- Economical: Zinc-coated materials economically diminish the repair time and cost due to rust damage, thus lowering the maintenance cost and operation cost of vehicles.
- Design Lightweight: Zinc-coated steel helps control the amount of steel used in vehicle production, contributing to weight reduction and improved fuel efficiency.
- Environmentally Friendly: Being recyclable, zinc coatings are an environmentally friendly option for automotive production, still meeting environmental requirements.
The benefits explain why zinc-coated steel is an absolute necessity in modern automotive engineering, enabling vehicles to maintain their quality, safety, and performance throughout their respective lifetimes.
Surface Treatment Techniques for Enhanced Durability
Certainly! When aiming for surface finishes for higher durability, I would consider galvanizing, plating, and powder coating. These methods serve to enhance the material’s resistance to corrosion, wear, and other environmental factors. Each technique is applied based on the needs to meet the expected degree of service life and performance of the coated surface under tough working conditions.
Applications of HSLA HX420LAD Coil
Application Area | Key Points |
---|---|
Automotive Industry | Structural reinforcements (e.g., chassis, cross-members) |
Crash-resistant parts (e.g., impact beams, side intrusion bars) | |
Body panels (e.g., inner door panels, roof frames) | |
Seat rails and floor beams for durability | |
Industrial Equipment | Machine frames and supports |
Structural elements for heavy-duty machinery | |
Enclosures and housings for industrial systems | |
Construction | Modular building frames and roofing systems |
Load-bearing wall panels and support beams | |
Cold-formed profiles for lightweight structures | |
Storage Systems | Racks, shelves, and pallet systems requiring high load capacity |
Container panels for durable, weather-resistant storage |
Use in the Automotive Industry
HX420LAD coil is the backbone, especially when automotive applications are considered, with a high-strength-to-weight ratio, corrosion resistance, and formability. Here are the five main applications of HX420LAD coils in the automotive sector:
- Structural Components
- HSLA HX420LAD coils are frequently used in the manufacture of structural components, such as chassis and frames, to impart durability and load-bearing ability.
- Data indicate that these steels can reduce vehicle weight by as much as 15% without compromising safety, thereby increasing fuel efficiency and mileage.
- Crash-Resistant Regions
- It is the most suitable material for use in the fabrication of crash-worthy zones, such as side impact beams and bumper reinforcements.
- It provides high tensile strength to secure the passengers during a collision.
- Body Panels
- Such HX420LAD coils are used to create lightweight body panels with improved aerodynamics, providing an excellent base for painting.
- Such activities can help in curb emissions in support of sustainability activities related to auto manufacturing.
- Suspension Systems
- The application of HSLA HX420LAD to create suspension components, such as control arms and suspension links, offers a combination of strength and flexibility that will withstand over time, even under harsh loads.
- Fuel Tanks
- The other preferred application of HX420LAD is in the safe production of fuel tanks due to its superior corrosion resistance.
- This ensures their reliability throughout the vehicle’s lifespan, even under severe environmental conditions.
All this beautifies the versatility and superiority of the HSLA HX420LAD coil in modern automotive engineering.
Advantages in Structural Applications
- High Strength-to-Weight Ratio
- The HX420LAD boasts an exceptional strength-to-weight ratio, enabling the creation of lighter structures with the same level of durability. This, in turn, reduces the overall material usage and increases the energy rating of the construction project.
- Corrosion Resistance
- Its corrosion resistance maintains the structural integrity for a long time, even when exposed to moisture, chemicals, or weather conditions. Hence, the maintenance cost for the life of the structure becomes less.
- Improved Formability
- The HX420LAD is characterized by excellent formability, allowing it to be transformed into complex geometries and developed into various structural designs. This property will assist architects and engineers in creating attractive designs.
- Superior Weldability
- Its high weldability level facilitates easy joining processes during construction, ensuring good bonding strength and reducing the likelihood of structural failures, even in critical load-bearing members.
- Cost-Effectiveness
- Even with such heavyweight properties, HX420LAD remains a very cheap option for structural purposes. Being durable minimizes the need for frequent repairs or replacements, resulting in significant long-term savings.
Innovative Uses in Other Industries
- Automotive Manufacturing
The HX420LAD is widely used in the automotive industry for manufacturing lightweight yet highly durable vehicle structures. Its high strength-to-weight ratio further enhances fuel efficiency, making the product compliant with stringent safety standards. Data suggest that an advanced high-strength steel makeup, such as HX420LAD, can significantly reduce a vehicle’s weight by nearly 25%, thereby considerably improving its performance.
- Appliance Manufacturing
This steel sheet is used in the manufacture of appliances, including washing machines and refrigerators. Its good formability and surface finish allow modern and sleek designs to evolve. Industry reports indicate that production costs are kept at least 15% lower when the HX420LAD is used, while upholding durability and quality.
- Construction and Infrastructure
It can be noted that HX420LAD were indispensable in the realization of infrastructure projects comprising bridges, skyscrapers, and other industrial buildings. While considering the structure, its ability to withstand loads and some environmental stresses ensured safety, while also attaining a longer lifespan. A 20 percent increase in resilience to extreme weather events was achieved by buildings constructed using HX420LAD compared to those built with conventional materials.
- Renewable Energy Sector
The high-strength steel is used in the construction of structures for wind turbines and supports for solar panels. Its aforementioned qualities – ability to resist harsh environmental conditions and heavy mechanical loads – ensure the longevity of renewable energy installations. According to industry data, the operational longevity of wind turbines is increased by 30% when HX420LAD is used in their manufacture.
- Agricultural Equipment
Agricultural apparatuses, such as tractors and harvesters, greatly appreciate the use of HX420LAD due to its exceptional toughness and wear resistance. The durability of the material results in reduced maintenance and operating costs. Farmers operating machinery with HX420LAD-obtained equipment report a decline of about 40% in repairs over 10 years.
References
- ProQuest:
- Article discussing the competition and demand for HSLA and AHSS grades, including HX420LAD.
- Link to source
- ResearchGate:
- A study on the HSLA industrial cycle and the production of HX420LAD steel grade.
- Link to source
- SpringerLink:
- Article on the new generation of economical automotive steel, including thermodynamic calculations for HSLA grades.
- Link to source
Frequently Asked Questions (FAQ)
What are the mechanical properties of HSLA HX420LAD steel?
HSLA HX420LAD steel exhibits excellent mechanical properties, including high yield strength and good formability. It is designed to meet the demands of automotive applications, ensuring durability and structural integrity.
What is the chemical composition of HSLA HX420LAD?
The chemical composition of HSLA HX420LAD includes a carefully balanced mix of elements that enhance its strength and corrosion resistance. This steel type typically contains low alloy content, providing the necessary characteristics for automotive applications.
How does coating affect the surface quality of HSLA HX420LAD coils?
Coating, such as hot-dip galvanization, significantly improves the surface quality of HSLA HX420LAD coils. It provides enhanced corrosion protection and ensures long-lasting performance in diverse environments, particularly in automotive applications.
What are the applications of HSLA HX420LAD steel coils?
HSLA HX420LAD steel coils are primarily used in automotive applications, where high-strength and lightweight materials are essential. The steel’s properties allow for the construction of structural components that require high yield strength and good weldability.
Can HSLA HX420LAD be welded?
Yes, HSLA HX420LAD is known for its good weldability, making it suitable for various welding techniques. This characteristic is crucial for applications that involve assembling structural components in the automotive industry.
What is the minimum yield strength of HSLA HX420LAD?
The minimum yield strength of HSLA HX420LAD is typically around 420 MPa, which ensures that the material can withstand significant stress while maintaining structural integrity in automotive applications.
What standards apply to HSLA HX420LAD steel?
HSLA HX420LAD steel is produced by standards such as EN 10346 and VDA 239-100, ensuring that it meets the required specifications for high-strength steel used in the automotive industry.
What is the difference between hot-rolled and cold-rolled HSLA coils?
Hot-rolled HSLA coils are produced at elevated temperatures, resulting in improved formability and lower residual stresses. In contrast, cold-rolled coils offer tighter tolerances and better surface finishes. Both types are suitable for various automotive applications depending on specific requirements.