When it comes to construction and concrete reinforcement, choosing the right rebar size is critical to the strength, safety, and durability of your project. Whether you’re working on a small residential foundation or a large-scale commercial structure, understanding rebar sizes and their applications is essential for achieving optimal results. This guide provides a comprehensive breakdown of rebar sizes, helping you make informed decisions based on your specific project needs. From understanding industry standards to exploring the properties of different rebar grades, we’ll equip you with the knowledge to select the best steel reinforcement for any construction scenario.
What is a rebar size chart and why is it important?
A rebar size chart is a reference tool that outlines the various diameters, weights, and properties of steel reinforcement bars used in construction. It is essential because it ensures accurate selection of rebar based on a project’s structural requirements. By using a rebar size chart, builders and engineers can determine the appropriate size and strength needed to achieve safety, durability, and efficiency in their designs.
Understanding the basics of rebar sizes
Rebar, short for reinforcing bar, is a steel bar or mesh used in concrete and masonry structures to provide additional strength and support under tension. Rebar sizes are denoted by numbers that represent their nominal diameter in eighths of an inch. For instance, a #4 rebar has a nominal diameter of 4/8 (or 0.5 inches). These sizes impact the weight, strength, and application of the rebar in construction.
Steel rebar is classified into various grades, which indicate its yield strength and composition. Common grades include 40, 60, and sometimes higher, depending on project needs. The choice of rebar size and grade depends on factors such as the type of structure, load requirements, and environmental conditions. Proper selection ensures optimal structural performance and longevity.
Most importantly, accurate knowledge of rebar sizes is critical for ensuring project safety and compliance with building codes. Using a standard rebar size chart enables builders to select the appropriate diameter and grade, preventing structural deficiencies while achieving cost-effective and efficient designs.
How rebar size affects construction projects
Rebar size plays a crucial role in determining a construction project’s strength, stability, and durability. Larger-diameter rebars can bear higher tensile loads, making them ideal for supporting substantial structural elements like beams, columns, and foundations. Conversely, smaller rebars are utilized in lighter structures or areas requiring fine detailing, as they provide flexibility and ease of placement.
Incorrect rebar size selection can lead to structural weaknesses, potentially causing safety hazards or increased maintenance needs over time. It also impacts the overall cost and efficiency of the project; oversizing may result in unnecessary expenses while undersizing can compromise integrity. Furthermore, rebar sizes must align with design specifications and building codes to ensure compliance and project success, highlighting the importance of precise engineering and planning.
The importance of selecting the appropriate rebar
Selecting the appropriate rebar is critical for ensuring any construction project’s safety, durability, and efficiency. Using the right size, type, and grade directly impacts the structural integrity of concrete, as rebar reinforces it to withstand various forces such as tension and compression. Improper selection could lead to cracks, reduced lifespan, and safety risks. Also, rebar must comply with building codes and design standards, balancing performance and cost-effectiveness. Common types include carbon steel, epoxy-coated rebar, and stainless steel, each suitable for specific environments and conditions. For instance, epoxy-coated rebar is ideal for high-corrosion environments, while stainless steel excels in providing long-term strength and resistance. Proper planning and consultation with engineering experts are essential to ensure the chosen rebar meets project requirements and avoids unnecessary expenses or liabilities.
How do I read and interpret a rebar size chart?
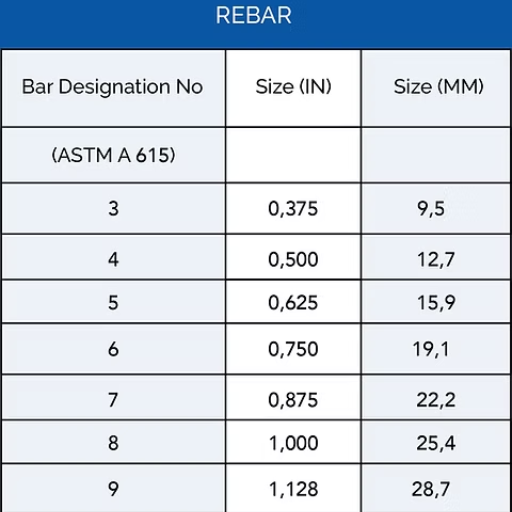
To read and interpret a rebar size chart, start by identifying the rebar size number, which corresponds to the diameter of the rebar in eighths of an inch. For example, a #4 rebar has a nominal diameter of 4/8 inch, or 0.5 inch. The chart typically also includes the rebar’s weight per linear foot, measured in pounds, which helps in estimating material requirements. Additionally, check for specifications such as grade, which indicates the yield strength, and ensure the rebar matches the project’s structural design needs. Always cross-reference with project standards and local building codes for accuracy and compliance.
Decoding nominal diameter and weight per foot
The nominal diameter of rebar refers to the approximate size designation used to identify the bar in construction, often measured in inches or millimeters. For example, a #4 rebar has a nominal diameter of 4/8 inch (0.5 inch), which correlates to its strength and suitability for various applications. The weight per foot of rebar is a critical parameter for estimating material requirements and is typically provided in pounds per linear foot. For instance, #4 rebar weighs approximately 0.668 pounds per foot. This weight is significant for calculations regarding load distribution and overall structural integrity.
Determine the correct nominal diameter and weight per foot to ensure the rebar aligns with your project’s structural specifications. Matching these values with the engineering design ensures compliance with safety standards and optimizes construction efficiency. For accuracy, always refer to manufacturer charts, local building codes, and project-specific requirements when assessing rebar.
Understanding rebar grade and tensile strength
Rebar grade refers to the classification of steel reinforcement based on its yield strength, which is the stress at which the material begins to deform plastically. Common grades include Grade 40, Grade 60, and Grade 75, where the number represents the yield strength in ksi (kilo pounds per square inch). Higher grades signify greater tensile strength, making them suitable for demanding applications.
Tensile strength, on the other hand, measures the maximum stress a material can withstand before breaking. It is a critical factor in ensuring that the rebar can effectively handle stretching forces, maintaining a project’s structural integrity. Selecting the appropriate grade and tensile strength depends on factors such as the load requirements, environmental conditions, and the type of structure being built.
Always consult project plans, engineering specifications, and material standards, such as those provided by ASTM International, to make an informed decision. This ensures compatibility with design requirements while adhering to safety and regulatory guidelines.
Comparing different sizes of rebar
Rebar comes in various sizes, each designated by a standard size number that reflects its nominal diameter in eighths of an inch. Key differences between rebar sizes relate to their strength, weight, and application. Smaller sizes, such as #3 and #4 rebar, are commonly used for lightweight projects like driveways or patios with relatively low load requirements. Medium sizes like #5 and #6 rebar are more suited for residential foundations or structural columns, offering a balance of strength and versatility. For heavy-duty applications such as bridges, large-scale infrastructure, or high-rise buildings, larger sizes like #8 through #11 are necessary due to their superior tensile strength and load-bearing capabilities.
Factors such as project specifications, structural load demands, and budget must be carefully evaluated when selecting the appropriate rebar size. Additionally, consulting with engineering standards such as those outlined by the ACI (American Concrete Institute) ensures compliance with technical and safety requirements for optimal performance.
What are the most common rebar sizes and their applications?
Due to their versatility and availability, rebar sizes #3, #4, and #5 are widely used in residential and commercial construction.
#3 Rebar is typically used for smaller-scale projects, such as driveways, patios, and light concrete slabs, where lighter loads are expected.
#4 Rebar is commonly employed in walls and slabs for residential and commercial foundations, balancing strength and flexibility for medium-load applications.
#5 Rebar is favored in heavy-duty applications such as bridges, multi-story buildings, and industrial structures due to its robust load-bearing capacity.
Beyond these, larger sizes like #6 and #8 are used in highly demanding infrastructure projects, providing the additional strength required for bridges, highways, and large-scale construction. Proper selection ensures structural integrity and longevity.
Popular rebar sizes for residential construction
The most frequently utilized rebar sizes for residential construction are #3, #4, and #5. These sizes adequately fulfill the structural requirements of an average home and are economical.
#3 Rebar is the lightest of all and is ideal for reinforcement in less demanding projects like sidewalks, patios, driveways, and slabs. It is best used in structures subjected to light or moderate weight.
#4 Rebar is sufficiently strong and flexible. It is widely used in the construction of walls, footings, and even residential foundation slabs and beams, as it enhances the support offered by walls.
#5 Rebar is less common, but it is encountered in heavy residential projects such as walls that need retaining, increased footings, or any other structures that would be expected to take on greater loads.
The choice of rebar size is influenced chiefly by the design blueprints, local building regulations, and the loads to be supported. Thus, an engineer’s advice would be useful in choosing the right size, especially when aiming for safety and performance.
Commercial and industrial rebar size requirements
Due to the scale and structural demands of commercial and industrial projects, the required rebar sizes tend to be significantly larger and more diverse. Typically, #6 Rebar through #18 Rebar are commonly utilized in these applications, given their ability to handle higher loads and provide added reinforcement. Larger rebar diameters ensure structural integrity under immense stress for extensive infrastructure projects like bridges, high-rise buildings, and highway pavements.
The choice of rebar size in these cases is determined by engineering specifications, as well as industry standards like ASTM requirements, to ensure compliance and safety. For instance, #18 Rebar is often used in critical areas of major infrastructure projects where maximum strength is essential. It’s vital to collaborate with experienced engineers and refer to project plans to confirm the ideal rebar size, ensuring the structure can withstand both current and future stresses effectively.
Specialized rebar sizes for unique projects
Specialized rebar sizes are often required for unique construction projects that demand tailored solutions to meet specific structural needs. For example, smaller rebar sizes such as #3 or #4 are typically utilized in detailed work like residential construction or tightly confined spaces due to their flexibility and ease of use. On the other hand, heavy-duty projects like bridges, tunnels, and skyscrapers rely on larger sizes, such as #14 or #18, to provide unparalleled strength and durability. Some custom rebar also features unique coatings, such as epoxy or galvanized finishes, to enhance corrosion resistance in environments with high moisture or chemical exposure. Selection of specialized rebar is determined by the project’s particular load requirements, regional construction codes, and long-term performance goals.
How do I choose the right rebar size for my project?
When selecting the right rebar size for your project, several factors should be considered to ensure structural integrity and compliance with construction standards. Start by assessing the load requirements and stress levels the structure will endure. Review the project’s design specifications and regional building codes, as these often dictate minimum size standards. Also, consult a structural engineer to determine the optimal rebar diameter and grade suited for your specific application. Balancing cost, durability, and structural needs will lead to an appropriate and efficient rebar selection.
Factors to consider when selecting rebar
- Load and Stress Requirements
Evaluate the expected loads and stress levels the structure will face. This includes understanding tensile strength, compression, and shear forces, which influence the appropriate rebar grade and size.
- Environmental Conditions
Consider the environment where the rebar will be placed. For corrosive environments, like coastal areas or regions with heavy use of deicing salts, epoxy-coated or stainless steel rebar may be necessary to prevent rust and ensure longevity.
- Building Codes and Design Specifications
Always adhere to regional building codes and project-specific specifications. Codes provide essential guidelines for minimum rebar size, spacing, and placement to ensure structural safety and compliance.
- Type of Concrete Structure
Different structures, such as beams, columns, slabs, or foundations, require specific rebar configurations in terms of size, spacing, and strength. Analyzing the type of structure will help determine the right reinforcement.
- Budget and Cost Efficiency
Selecting rebar that meets structural needs without excessive oversizing can balance cost and performance. Rebar type, coating, and grade can all impact overall project costs.
By prioritizing these factors, you can ensure a safe, durable, cost-effective rebar selection for your construction project.
Matching rebar size to structural requirements
Choosing the correct rebar size ensures structural integrity and compliance with design specifications. The rebar size directly correlates to the structure’s load-bearing capacity. Smaller sizes, such as #3 or #4, are commonly used for light structural components like slabs and driveways, while larger sizes, such as #6 to #18, are suited for heavy-load applications like columns, beams, and bridges.
Structural requirements are determined based on factors like the type of structure, expected load, and environmental conditions. Consulting code guidelines, such as the American Concrete Institute (ACI) standards, helps calculate the required rebar size and placement. Using engineering software or professional input can further simplify decisions and improve accuracy. Ultimately, the goal is to balance safety, efficiency, and cost-effectiveness in rebar selection.
Consulting with professionals for rebar selection
When selecting a rebar, I rely on professional consultation to ensure that decisions align with current standards and best practices. Experts help evaluate load requirements, structural types, and environmental influences while referencing trusted guidelines such as ACI standards or local building codes. They also utilize advanced tools and software to analyze project specifications, ensuring precise rebar sizing and placement. This approach optimizes safety and efficiency and helps manage costs effectively.
What are the different types of rebar available?
Below is a list of the various kinds of rebar and their applications:
Carbon Steel Rebar – As the industry standard rebar, it is known for its high strength-to-cost ratio.
Stainless Steel Rebar – Best for highly corrosive structural applications due to its corrosion resistance.
Epoxy-Coated Rebar—This type of rebar is used in marine projects or other structures exposed to salt. Its coating protects it from corrosion.
Glass-fiber-reinforced polymer (GFRP) Rebar is used in applications that require non-metallic reinforcement. It is lightweight and does not corrode.
Welded Wire Fabric (WWF)—This type of fabric consists of prefabricated steel mesh and is Used in smaller projects, such as slabs and walls.
All types of rebar differ in cost, durability, and performance level, tailoring them to specific project requirements.
Carbon steel vs. stainless steel rebar
When comparing carbon steel and stainless steel rebar, the primary considerations involve cost, durability, and resistance to corrosion. Carbon steel rebar is the most commonly used due to its affordability and solid strength, making it a cost-effective choice for many standard applications. However, it is prone to corrosion over time, especially in environments exposed to moisture, salt, or chemicals.
On the other hand, stainless steel rebar offers superior corrosion resistance, making it suitable for marine environments, bridge decks, or other structures exposed to harsh conditions. While the initial cost of stainless steel rebar is significantly higher than carbon steel, its long-term durability and reduced maintenance needs often justify the investment for critical projects. Choosing between the two depends largely on the project’s exposure to corrosive elements, budget constraints, and expected lifespan of the structure.
Epoxy-coated and galvanized rebar options
When considering epoxy-coated and galvanized rebar, I focus on their unique properties and how they align with the needs of my projects. Due to its protective coating, epoxy-coated rebar is highly resistant to corrosion, making it a popular choice for structures exposed to moisture or de-icing chemicals. However, care is essential during handling and installation to avoid damaging the coating, as even small chips can compromise its effectiveness.
Galvanized rebar, on the other hand, provides robust protection through its zinc coating, which prevents rust even if minor scratches occur. It requires less careful handling than epoxy-coated rebar, offering an advantage in projects where durability and ease of use are priorities. My choice often depends on the level of exposure to corrosive elements, cost considerations, and the specific durability requirements of the structure. Both options are excellent for extending the life span of reinforced concrete, especially in challenging environments.
Innovative rebar materials: fiberglass and low-alloy steel
Fiberglass Rebar
Fiberglass rebar, also known as glass fiber-reinforced polymer (GFRP) rebar, is a cutting-edge material gaining popularity due to its unparalleled corrosion resistance. Unlike traditional steel rebar, fiberglass is non-conductive and non-magnetic, making it ideal for structures such as bridges, seawalls, and facilities containing sensitive equipment. It is lightweight yet robust, allowing for easier handling and installation. However, its higher initial cost and lower resistance to fire compared to steel can be limiting factors in some projects.
Low-Alloy Steel Rebar
Low-alloy steel rebar enhances strength and corrosion resistance while maintaining affordability. By incorporating small quantities of elements like chromium, nickel, or vanadium, this material delivers improved durability in aggressive environmental conditions, such as those found in marine or industrial settings. It offers a practical balance between performance and cost, making it a viable alternative for infrastructure projects that require long-term reliability without significantly increasing expenses.
How does rebar grade affect its performance and selection?
Rebar grade is crucial in determining its performance and suitability for specific applications. The grade, often indicated by a number, reflects the yield strength of the rebar in pounds per square inch (psi). Higher-grade rebar provides more excellent stability and is ideal for heavy-load structures like high-rise buildings or bridges. Conversely, lower-grade rebar suits less demanding applications where flexibility and cost-effectiveness are priorities. Additionally, the rebar grade influences factors like ductility, ease of welding, and resistance to environmental stressors, all of which must be considered when selecting the appropriate material for a project.
Understanding Grade 40 and Grade 60 rebar
Most construction work incorporates Grade 40 and Grade 60 rebar, the two most common reinforcing bars. Their main difference is in the amount of tensile and yield strength in each one. Since Grade 40 rebar has a yield strength of 40,000 psi, it is commonly used in light to medium construction projects such as residential buildings. It is easier to bend, cut, or weld due to its lower strength, ductility, and deformability than Grade 60. This ductility caters to more simplistic structural needs.
In comparison, Grade 60’s yield strength of 60,000 psi allows it to be used for heavy-duty applications like high-rise buildings, bridges, and other industrial projects. It offers superior durability, high load-bearing strength, and resistance to harsh environmental conditions. However, its weaker ductility compared to Grade 40 means that it is considerably less flexible, making alteration much more difficult.
Along with the project’s design, environmental conditions, and budget, the grade decision also requires careful evaluation. Unlike Grade 40 and Grade 60, both meet the standard construction code requirements.
High-strength rebar options for demanding projects
When selecting high-strength rebar for challenging projects, it is essential to prioritize factors like structural demands, environmental conditions, and compliance with construction codes. Grade 60 rebar remains the industry standard due to its yield strength of 60,000 psi, excellent durability, and resistance to environmental pressures, making it ideal for bridges, skyscrapers, and earthquake-prone areas. For projects requiring even greater strength, Grade 75, Grade 80, and Grade 100 rebars are advanced options, with higher tensile strength levels suited for heavily loaded structures or limited-space applications.
Each type of rebar is tailored for specific uses. Epoxy-coated or stainless steel rebar offers superior corrosion resistance, which is critical for marine or high-humidity environments. Meanwhile, micro-alloyed and low-alloy steel rebars combine strength with weldability for custom installations. Budget considerations and specific project designs should guide the final choice, balancing performance with cost efficiency.
Matching rebar grade to project specifications
Selecting the correct rebar grade for a construction project depends on load requirements, environmental conditions, and structural design. The most widely used Grade 40 and Grade 60 rebars are ideal for general-purpose applications due to their reliable strength and availability, for projects demanding higher tensile strength, such as high-rise buildings or infrastructure like bridges, Grade 75, Grade 80, and Grade 100 rebars are recommended. These grades deliver enhanced performance in heavy-load or space-constrained scenarios.
Environmental conditions play a critical role in specifying rebar grades. For structures exposed to corrosive elements, such as coastal areas or chemical plants, epoxy-coated or stainless steel rebars are essential due to their corrosion resistance. Similarly, in seismic zones or where flexibility in structural design is vital, low-alloy and micro-alloy steel rebars provide a combination of durability and weldability.
Collaborate with structural engineers to analyze load demands, budget constraints, and environmental considerations to ensure the chosen grade aligns with project requirements. Properly assessing these factors helps ensure long-term structural integrity and cost-effective performance, especially for safety-critical applications.
References
Frequently Asked Questions (FAQ)
Q: What are the different rebar types available?
A: Rebar types include black rebar, epoxy coated rebar, and stainless steel rebar. Each type is suited for different environmental conditions and project requirements.
Q: How do I choose the right steel rebar sizes for my project?
A: Choosing the correct size of rebar for your project depends on factors like the load requirements, structural design, and specific engineering standards. Consulting a structural engineer can help ensure the right choice.
Q: What type of steel is commonly used for rebar?
A: Rebar is commonly made from carbon steel due to its strength and cost-effectiveness. Stainless steel rebar provides additional corrosion resistance and is used for projects in harsh environments.
Q: Why is steel reinforcement important in construction?
A: Steel reinforcement, such as rebar, is crucial because it strengthens concrete structures, helping them withstand tensile forces and preventing cracks and failures.
Q: What standards for rebar should I be aware of?
A: Rebar sizes are standardized according to various standards, such as ASTM in the United States. These standards ensure consistency in the cross-sectional area of the rebar and its performance.
Q: How is the grade of rebar determined?
A: The grade of rebar is determined by its yield strength, which is the stress at which it begins to deform plastically. For example, Grade 80 rebar has a minimum yield strength of 80,000 psi.
Q: What are the advantages of using epoxy coated rebar?
A: Epoxy coated rebar is used to protect against corrosion, especially in environments exposed to moisture and salt, such as bridges and marine structures.
Q: When should I consider using stainless steel rebar?
A: Stainless steel rebar should be considered for projects where long-term durability and resistance to corrosion are critical, such as in coastal or chemical-exposed environments.
Q: How does rebar play a role in preventing structural failures?
A: Rebar can help prevent structural failures by providing tensile strength to concrete structures, which are naturally strong in compression but weak in tension.