Stainless steels are highly versatile and have found application in a multitude of industries. Among the many types of stainless steel, 410s stainless steel stands out for its starkly contrasting properties. 410S stainless steel may be the item you’re looking for, offering exceptional strength, durability, and corrosion resistance at a reasonable price. What, then, really sets this alloy apart? We will examine the distinguishing features of 410 stainless steel, its typical applications across various industries, and its competitiveness in comparison to similar stainless steel grades. Whether you are an engineer, a product manufacturer, or just simply an inquisitive material science student, this detailed article will cross-reference all the details you might need to get to know about this extraordinary material.
Introduction to 410s Stainless Steel
410S stainless steel is a low-carbon version of standard 410 stainless steel, offering improved resistance to corrosion and better weldability. The alloy retains decent strength and durability, yet it does not tend to harden, unlike other martensitic stainless steels. It is composed of iron, chromium, and a very low carbon content, making it suitable for use in applications requiring resistance to oxidation at high temperatures and mild corrosion resistance. Frequently applied in the automotive, construction, and petrochemical industries, 410 stainless steel is appreciated for its affordable balance of performance and versatility.
What is 410s Stainless Steel?
410S stainless steel is a ferritic stainless steel that offers moderate corrosion resistance, good oxidation resistance, and enhanced formability. It is used in applications where good stress resistance is required in various industries.
Composition and Alloy Characteristics
410s stainless steel mainly contains iron and chromium, along with trace elements that enhance its properties.
The approximate chemical composition of this grade is as follows:
- Chromium: 11.5-13.5% Chromium imparts basic resistance to corrosion and oxidation, which is core to many industrial applications.
- Carbon: ≤ 0.08% Less Carbon than regular type 410 stainless steel, which would have better weldability and a lower risk of hardness-induced brittleness.
- Manganese: ≤ 1% The Manganese mainly increases the strength and durability of the alloy.
- Silicon: ≤ 1%. Silicon contributes to oxidation resistance, primarily at elevated temperatures.
- Nickel: ≤ 0.6% The trace amount of Nickel might be incorporated for slightly enhanced toughness and corrosion performance.
- Phosphorus: ≤ 0.04% Low values of phosphorus are maintained to enhance the material’s ductility.
- Sulfur: ≤ 0.03% Sulfur is kept to a minimum to allow good machinability without sacrificing corrosion resistance.
410S stainless steel is specifically designed to offer good weldability and stability compared to other 400 series stainless steels, particularly for applications subjected to thermal cycling. Mechanical properties typically include:
- Tensile Strength: About 415-655 MPa
- Yield Strength: About 240-450 MPa
- Elongation (in 2 inches): ~20%
- Hardness (Brinell): 180 max (annealed).
This particular set of compositions and their related properties makes 410S stainless steel a low-cost option for moderately corrosive environments, offering excellent processing ability, particularly for exhaust systems, heat exchangers, and architectural applications.
Comparison with Other Stainless Steels
Property | 410S Stainless Steel | 410 Stainless Steel | 416 Stainless Steel | 430 Stainless Steel |
---|---|---|---|---|
Carbon Content | ≤0.08% | 0.08–0.15% | ~1% | Low |
Chromium Content | 11.5–13.5% | 11.5–13.5% | 13% | 16–18% |
Hardness | Lower | Higher | Moderate | Low |
Strength | Moderate | High | Moderate | Low |
Ductility | Higher | Lower | Moderate | High |
Weldability | Excellent, no preheat needed | Requires preheat and post-weld tempering | Poor | Good |
Corrosion Resistance | Similar to 410, better after welding | Fair, reduced near welds | Moderate | Good |
Heat Resistance | Up to 1300°F (705°C) | Up to 1200°F (649°C) | Up to 1247°F (675°C) | Up to 1499°F (815°C) |
Applications | Heat exchangers, welded parts, petrochemical | Cutlery, valves, turbine blades | Gears, pumps, automatic screw machines | Automotive trim, appliance components |
Magnetic | Yes | Yes | Yes | Yes |
Fabrication Ease | Easy to shape and weld | Harder to shape, requires heat treatment | Moderate | Easy |
Properties of 410s Stainless Steel
The key properties of 410s Stainless Steel are:
- Corrosion Resistance: Moderate resistance to atmosphere and mild corrosive environments.
- Mechanical Strength: Exhibits good tensile strength and durability, with a tensile strength generally ranging from 240 to 450 MPa.
- Thermal Stability: Remains stable and resistant to oxidation at elevated temperatures.
- Workability: Easy to shape and weld for a variety of fabrication.
- Hardness: Possesses an ultimate Brinell hardness of 180 in the annealed condition.
These characteristics make 410 stainless steel a good all-around and economical choice for industrial and structural applications.
Mechanical Properties and Hardness
410S stainless steel is known for its excellent balance of mechanical properties and, therefore, stands chosen by various industries for various applications. Following are the process parameters and data regarding mechanical properties and hardness:
- Tensile Strength: 485-690 MPa is the tensile strength range provided by 410S stainless steel, strong enough to be employed in structural and industrial uses.
- Yield Strength: Yield strength in the range of 275-450 MPa is adequate in resisting deformation under load from 410S.
- Hardness: The Brinell hardness of annealed 410S stainless steel ranges from 170 to 180 BHN, providing moderate abrasive resistance and machinability.
- Elongation: It exhibits an elongation of approximately 20% in 2 inches, making it sufficiently ductile for forming and shaping operations.
- Impact Strength: Good in toughness and fair in resistance to impact under low and room temperature.
- Density: Somewhat lightweight at 7.75 g/cm³ while maintaining strength and formability.
- Thermal Expansion Coefficient: It has a thermal expansion coefficient of 10.2 × 10⁻⁶/K, which addresses any concerns about dimensional stability in high-temperature working environments.
This information suggests that 410S stainless steel is somewhat softer than its martensitic counterparts, but it offers superior durability and workability. These qualities make 410S a good choice where corrosion resistance and moderate mechanical strength are paramount. Verify standards, such as ASTM A240, to finalize exact engineering needs and confirm suitability for the intended applications.
Corrosion Resistance and Oxidation Resistance
410S stainless steel, with its excellent corrosion and oxidation resistance, is the alloy that meets all these requirements. These characteristics stem from a balanced chromium content and a stable microstructure. The various facets of its performance are highlighted as follows:
General Corrosion Resistance
The steel withstands mild atmospheric and chemical environments. It performs well in environments with low chloride exposure or acidic conditions, thereby preventing surface erosion and pitting.
Oxidation Resistance at High Temperature
Resistance to scaling or mass loss of mechanical properties at continuous service temperature of 1300°F (700°C), allowing it to operate reliably in high-temperature environments.
Resistance in Wet Corrosive Environments
Performs well in application environments with a moderate amount of moisture, such as mild industrial atmospheres and freshwater environments, resisting surface rusting and structural degradation.
Chloride Stress Corrosion Cracking Resistance
It is not good for high chloride concentration environments, but in moderately saline environments, it exhibits sufficient resistance to stress corrosion cracking.
Sulfurous Atmosphere Resistance
Moderate resistance in sulfurous atmospheres, often present in industrial applications, is due to its resistance to oxidation and scaling by sulfides, such as those found in boiler or chemical plants.
Hence, these capabilities make 410S stainless steel a robust contender for applications that demand longevity with moderate environmental resistance. Always refer to industry standards when selecting the best material for your application.
Formability and Fabrication Techniques
I find the formability of 410S in stainless steel to be moderate but sufficient for basic fabrication techniques. Bending, welding, and machining are not so difficult if you follow appropriate methods to avoid undesirable side effects such as cracking. I always employ preheating and post-weld heat treatments in welding procedures to improve the integrity of the metallic material and minimize residual stresses. Additionally, recommended tooling conditions and operational parameters are employed to ensure accurate results without compromising material performance.
Applications and Use Cases
Due to its strength and durability, this material is widely used in building construction, car manufacturing, shipbuilding, and aerospace. It finds crucial application, especially in structural components, heavy machinery, and pressure vessels, where there is a need for stress resistance and reliability. Due to its greater flexibility during fabrication, it is typically preferred in applications where on-site work is prevalent or in harsher environments.
Common Industries Utilizing 410s
- Construction Industry
Due to its strength and resistance to wear, 410 steel is commonly used in construction for framework, reinforcement, and structural elements. It is best suited for applications supporting heavy loads, such as bridges, buildings, and industrial facilities.
- Automotive Industry
The material finds usage in automotive manufacturing for exhaust systems, engine parts, and drivetrain components. The durability and resistance to temperature changes in 410 steel make it an ideal material for vehicles.
- Aerospace Industry
Due to its good strength-to-weight ratio and excellent resistance to stress and corrosion, 410 steel is utilized by the aerospace industry for aircraft landing gear, engine components, and even structural materials in aircraft construction.
- Shipbuilding Industry
Due to its toughness and corrosion resistance, 410 steel is extensively used in shipbuilding for hulls, deck structures, and other components exposed to marine weather.
- Oil and Gas Industry
The oil and gas industry employs 410 steel in pipes, valves, and pressure vessels. Its resistance to extreme temperatures and pressures ensures optimal performance under rigorous conditions, thereby prolonging the equipment’s life.
Specific Products Made from 410s Stainless Steel
- Industrial Blades
Due to their superior hardness and wear resistance, 410s stainless steel blades are popularly chosen. Industries employ blades in the food processing, paper industry, and recycling sectors.
- Surgical Instruments
Surgical instruments have an application of 410s stainless steel in manufacturing in scalpels, forceps, and scissors. The stainless steel retains its sharp edges; therefore, it is resistant to corrosion, sterilization, and repeated use.
- Pump Shafts
This stainless steel is commonly employed for pump shafts in chemical processing and water treatment due to its mechanical strength and wear resistance, providing longer life to the pump shafts in high-torque environments.
- Automotive Components
For parts in automotive cushioning, like 410s, stainless steel valve seats and bushings are used. Due to its strength and heat resistance, 410 stainless steel can withstand high operating temperatures and stresses imposed on vehicle systems.
- Fasteners
Bolts, nuts, and screws fabricated from 410s stainless steel are used in construction, aerospace, and marine industries. These fasteners will have both tensile strength and corrosion resistance, enabling them to meet environmental and structural requirements in a challenging manner.
Advantages of Using 410s in Exhaust Systems
Key Point | Advantage |
---|---|
Weldability | Excellent, no preheating is required |
Corrosion Resistance | Resists rust in exhaust gas environments |
Heat Resistance | Operates up to 1300°F (705°C) |
Ductility | High, allows easy shaping and forming |
Oxidation Resistance | Resists scaling at high temperatures |
Cost Efficiency | Lower fabrication costs, minimal welding steps |
Durability | Long-lasting in high-heat, corrosive conditions |
Magnetic Properties | Suitable for magnetic applications if needed |
Environmental Suitability | Performs well in mild chemical and atmospheric conditions |
Fabrication Ease | Easy to process for complex exhaust designs |
Comparative Analysis
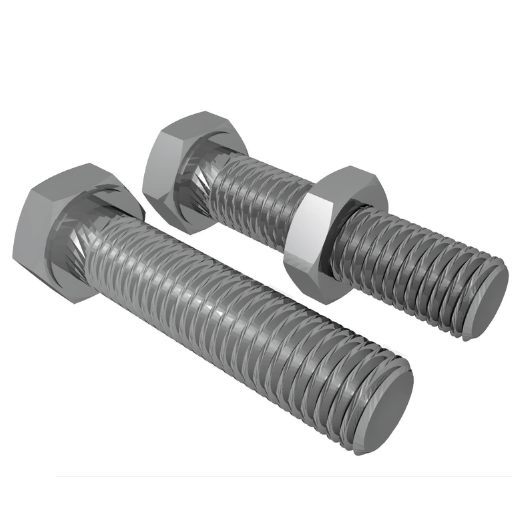
410s confers certain advantages when compared with the other materials customarily used in exhaust systems. First of all, corrosion resistance in atmospheric conditions is higher for 410S than for mild steels, thus ensuring better performance when subjected to high temperatures and moisture. Next, 410s offers a higher internal resistance to heat compared to aluminum; here, internal resistance refers to the degradation that occurs over time. High-grade alloys are, of course, superior to 410s when it comes to enforcement and durability, although 410s tend to win out in weighing out between performance and cost. Because of this influential property, 410s emerges as the best candidate for the design of exhaust systems in terms of reliability and economic considerations.
410s vs. 430 Stainless Steel
Property | 410S Stainless Steel | 430 Stainless Steel |
---|---|---|
Carbon Content | ≤0.08% | Low |
Chromium Content | 11.5–13.5% | 16–18% |
Hardness | Lower | Low |
Strength | Moderate | Low |
Ductility | Higher | High |
Weldability | Excellent, no preheat needed | Good |
Corrosion Resistance | Similar to 410, better after welding | Better in atmospheric conditions |
Heat Resistance | Up to 1300°F (705°C) | Up to 1499°F (815°C) |
Applications | Exhaust systems, heat exchangers, petrochemical | Automotive trim, appliances, chemical equipment |
Magnetic | Yes | Yes |
Fabrication Ease | Easy to shape and weld | Easy |
410s vs. 304 and 316 Stainless Steels
Property | 410S Stainless Steel | 304 Stainless Steel | 316 Stainless Steel |
---|---|---|---|
Carbon Content | ≤0.08% | ≤0.08% | ≤0.08% |
Chromium Content | 11.5–13.5% | 18–20% | 16–18% |
Nickel Content | None | 8–10.5% | 10–14% |
Molybdenum Content | None | None | 2–3% |
Corrosion Resistance | Moderate, better after welding | High | Excellent, especially in chlorides |
Strength | Moderate | Moderate | Moderate |
Hardness | Lower | Lower | Lower |
Ductility | Higher | High | High |
Weldability | Excellent, no preheat needed | Excellent | Excellent |
Heat Resistance | Up to 1300°F (705°C) | Up to 1500°F (815°C) | Up to 1600°F (870°C) |
Applications | Exhaust systems, heat exchangers, petrochemical | Food processing, kitchen equipment | Marine, chemical, medical applications |
Magnetic | Yes | No | No |
Fabrication Ease | Easy to shape and weld | Easy | Easy |
When to Choose 410s Over Other Alloys
Based on deciding whether 410 is appropriate relative to other alloys, such as 304 and 316, my first thought is structured around the specifics of the application needs. If a project requires weldability, moderate corrosion resistance, and sufficient heat resistance up to 1300°F, 410S is a good choice. 410s are also chosen for an exhaust system or petrochemical application where its magnetic property, as well as ease of fabrication, offers an edge. However, depending on the environment, if more corrosion resistance or higher temperature resistance is required, then I must go for 304 or 316.
Conclusion
Depending on the environment and performance requirements of the application, a specific material will be chosen. For medium corrosion resistance, weldability, and heat resistance up to 1300°F, 410S is a good selection, especially for exhaust systems or in petrochemical equipment. On the other hand, if the application requires higher resistance to corrosion or resistance to higher temperatures, stainless steel 304 or 316 can be used. Always consider the project’s unique requirements when selecting materials to achieve the best result.
Summary of Key Points
Material Selection Criteria:
The selection of an appropriate stainless steel depends upon specific environmental considerations and performance requirements. Factors such as corrosion resistance, temperature resistance, and weldability must be evaluated against the project’s specific requirements.
410S Stainless Steel:
- Best application for it is an environment that sustains mild corrosion and temperature resistance up to 1300°F (704°C).
- It finds use in exhaust systems, petrochemical equipment, and thermal environments due to its dependable performance.
304 and 316 Stainless Steel:
- 304 Stainless Steel is highly sought after for its exceptional corrosion resistance and excellent ability to interface with other materials. It is widely used in the food processing, automotive, and construction industries, as it can endure temperatures of up to 870°F (465°C) in continuous use.
- 316 Stainless Steel, being superior in corrosion resistance to 304, is preferred due to its enhanced resistance to chlorides and marine environments, making it the preferred choice for equipment subjected to salty or acidic environments. It also withstands continuous exposure to temperatures up to 925°F (496°C).
Statistical Insights:
- Present statistics reveal that 304 and 316 stainless steel combined make up more than 50% of all stainless steel applications worldwide, highlighting their widespread use in industries that are highly dependent on durability and chemical resistance.
- Research forecasts the stainless steel market to grow at an average CAGR of 5% between 2023 and 2030, primarily due to its widespread applications in construction, energy, and transportation.
Cost Consideration:
- 410S grade stainless steel is generally less expensive than the 304 and 316 grades, making it a more economical option when the project specification requires moderate performance.
- Initial expenditures made for higher-grade steel, such as 316, may help reduce maintenance costs in the long run, particularly in highly corrosive environments.
Choosing the correct stainless steel grade is a vital aspect of striking a delicate balance between performance, cost, and durability, ultimately leading to success in a project. One must always analyze the material properties in conjunction with the prevailing environmental and operational parameters of the application.
Future Trends in Stainless Steel Alloys
Looking ahead, my view is that the future alloys of stainless steel shall be more focused on sustainability and innovation. It appears that the trend is toward alloys that offer increased resistance to extreme environments while also reducing their environmental impact. From my perspective, recycling technologies and lightweight, high-strength alloys will be the key drivers in the industry in the long run. These technologies could extend the applications further and eventually make stainless steel more affordable and environmentally friendly.
Final Thoughts on the Importance of 410s
An intelligent composite, the 410 stainless steel alloy retains its strength in various industries due to its unique constitution, which combines wearability with strength, durability, and corrosion resistance. This martensitic stainless steel, which contains approximately 11.5% to 13.5% chromium, is heavily favored in applications where wear resistance is required, along with moderate corrosion protection. Its range of usages fits perfectly well in the aerospace, automotive, and construction sectors.
Recent trends indicate an upward demand for 410 stainless steel, with industries favoring materials that maintain their form and exhibit optimal performance under mechanical stress in extreme situations. For example, the global stainless steel market is projected to reach a value of $182 billion by 2030, at a CAGR rate of 5.9%. It is the 410-grade alloys that have become essential. Additionally, binders in heat treatment have been developed to achieve higher hardness and tensile strength in 410 alloys, making them increasingly suitable for cutting-edge applications such as turbine blades, medical instruments, and petrochemical pipelines.
Sustainability remains the theme in stainless steel production, with modern recycling techniques taken into consideration, which achieve a recycling rate of approximately 90% for stainless steel products. Hence, 410 stainless steel supports further industrial development, thereby ensuring that 410 stainless steel aligns well with global sustainability targets. These trends thus confirm the ongoing impetus of the 410s as the crossroads of performance, cost-effectiveness, and environmental responsibility.
References
- Material Science and Engineering Websites:
- Sandmeyer Steel: A professional source for information on 410S stainless steel.
- Industry Standards and Guidelines:
- ASME (American Society of Mechanical Engineers): For materials standards and specifications.
- CourseHero: GRA 410 Syllabus – This syllabus outlines an advanced digital graphic design course focusing on responsive web design and content management systems.
Frequently Asked Questions (FAQ)
What is Grade 410s Martensitic Stainless Steel?
Grade 410s is a martensitic stainless steel known for its good corrosion resistance and high strength. It is often used in applications where oxidation resistance and the ability to harden through heat treatment are required. This steel grade strikes a balance between hardness and toughness, making it suitable for a wide range of industries.
How does the Corrosion Resistance of 410s compare to Other Stainless Steels?
Grade 410s has moderate corrosion resistance compared to austenitic stainless steels like 304 and 316. While it is more resistant to corrosion than ferritic stainless steel, it is not as effective in highly corrosive environments. For applications with high exposure to corrosive substances, grades like 304 or 316 may be preferred.
What Are the Mechanical Properties of Martensitic Stainless Steel 410s?
The mechanical properties of Grade 410 stainless steel include high tensile strength and hardness, making it suitable for applications that require durability. Its yield strength typically ranges from 450 to 550 MPa, and it can be hardened through heat treatment to enhance its mechanical performance.
Can Grade 410s Be Used for Automotive Exhaust Applications?
Yes, Grade 410s can be used in automotive exhaust applications due to their ability to withstand high temperatures and their decent oxidation resistance. However, for optimal performance in corrosive environments, higher grades like 304 or 316 may be more effective.
What is the Difference Between 410s and 316 Stainless Steel?
Grade 410s is a martensitic stainless steel, while 316 is an austenitic stainless steel. The key differences lie in their corrosion resistance and mechanical properties. While 316 offers superior corrosion resistance due to its higher nickel content, 410s is more susceptible to corrosion but can be hardened effectively.
How Does Heat Treatment Affect the Hardness of 410s?
Heat treatment significantly increases the hardness of Grade 410 stainless steel. When subjected to heat treatment processes, such as quenching and tempering, the steel develops a martensitic structure, which enhances its hardness and strength, making it suitable for demanding applications.
Is Grade 410s Weldable?
Grade 410s can be welded, but care must be taken to avoid issues such as cracking. It is recommended to use specific welding techniques and fillers compatible with martensitic stainless steels to ensure strong joints and minimize the risk of corrosion at the weld sites.
What Applications Commonly Use 410s Stainless Steel?
Grade 410s stainless steel is utilized in a wide range of applications, including cutlery, valves, pumps, and various components in chemical processing equipment. Its combination of strength, hardness, and moderate corrosion resistance makes it suitable for both industrial and consumer products.