Carbon steel has been historically favored for numerous applications across various industries, ranging from construction to cookware. The Achilles’ heel of this metal, however, is the formation of rust, which can weaken the metal’s structure or degrade its external appearance, thereby reducing its lifespan if not periodically addressed. Understanding the hows and whys behind the rusting of carbon steel is, therefore, essential if one intends to keep the metals in good shape for use. This article takes you through the rusting mechanism, practical preventive methods, and maintenance approaches. Working in carbon steel-related industrial setups or wanting to protect your household tools? This guide intends to help you with what is necessary to maintain carbon steel in top shape.
The Science of Carbon Steel and Rust Formation
When carbon steel is exposed to oxygen and moisture, it undergoes a chemical reaction called oxidation, resulting in the formation of rust. The alternative name for rust is iron oxide. Rust sets in when iron in carbon steel reacts with water and oxygen, weakening the carbon steel and compromising its surface. Humidity and exposure to water accelerate the rusting process. The absence of enough protective elements, such as chromium, renders carbon steel vulnerable to rust. The process can be aggravated in the presence of salt or acidic environments, so the steel must be adequately maintained to prevent deterioration.
How Carbon Steel Rusts
Iron on carbon steel rusts when it reacts with water and oxygen, producing iron oxides. The process progresses rapidly in humid environments with the presence of salts or acids, unless protected by surface coatings or surface treatments.
The Chemical Process Behind Rusting
The rusting process has been understood as an example of an electrochemical reaction. Contact between iron, water, and oxygen results in the formation of hydrated iron(III) oxide, commonly known as rust. It starts at the surface of the metal. Below is a brief account of the reactions involved:
- Oxidation – At anodic sites on the metal surface, iron is oxidized to ferrous ions:
Fe → Fe²⁺ + 2e⁻
- Reduction – The electrons from the iron then flow to a cathodic site, where an aqueous solution containing dissolved oxygen is reduced to hydroxide:
O₂ + 4H⁺ + 4e⁻ → 2H₂O
(in neutral/basic environment, the reaction becomes O₂ + 2H₂O + 4e⁻ → 4OH⁻)
- Formation of Hydrated Iron Oxide- These ferrous ions from the cathodic area will react with the hydroxide ions and form ferrous hydroxide. This in fact, is then oxidized further in the presence of oxygen and water to give hydrated iron(III) oxide (Fe₂O₃.xH₂O), which is the reddish-brown rust observed on cast steel and other back-metal surfaces:
4Fe(OH)₂ + O₂ + 2H₂O → 4Fe(OH)₃ → 2Fe₂O₃·H₂O
Environmental Factors Influencing Rusting
Data support the notion that rusting occurs relatively quickly in most atmospheres with varying degrees of humidity or in specific places exposed to saltwater. Such as:
- Humidity: Scientists have demonstrated that rust forms very rapidly once relative humidity crosses 60 percent. Below this value, almost no rust formation takes place.
- Salt Effect: Chloride ions, a common constituent of seawater, can exacerbate the situation by increasing conductivity and disrupting oxide layers.
- For example, in a marine environment, corrosion rates for steel can reach up to 1.5 mm per year, compared with less than 0.1 mm in dry inland areas.
Prevention Strategies
To prevent rusting, modern methods such as galvanization (zinc coating), painting, and the use of inhibitors are employed. In extreme climatic conditions, surface treatments with chromium and weathering steel offer increased resistance. With an understanding of the chemistry involved, industries can work towards preventing rust in various applications.
Factors That Contribute to Corrosion
Environmental and other material-related factors contribute to the occurrence of corrosion. The following are five key contributors to the process:
- Moisture and Humidity
High atmospheric moisture is directly proportional to the acceleration of corrosion, especially in coastal and tropical areas. Water acts as an electrolyte, assisting the electrochemical reactions in rust formation.
- Temperature Variations
On many occasions, temperature variation induces the formation of condensation drops on the metal surface, which ultimately leads to the accumulation of water, thereby completing the corrosion mechanism. Higher temperatures also increase the rate of chemical reactions.
- Salt and Chlorides
Salt, especially in marine environments or from the de-icing of roads, will exacerbate the effects of corrosion due to its capacitive nature in retaining moisture and enhancing the electrical conductivity of the corrosion solution.
- Pollutants
Industrial pollutants, such as sulfur dioxide (SO₂) and nitrogen oxides (NOₓ), react with moisture to form acidic solutions that accelerate the corrosion of metals.
- Material Properties
A metal’s composition and surface treatment, along with its microstructural elements, play a vital role on its corrosion resistance. Stainless steel, for example, contains chromium, which increases its resistance.
Preventing Carbon Steel from Rusting
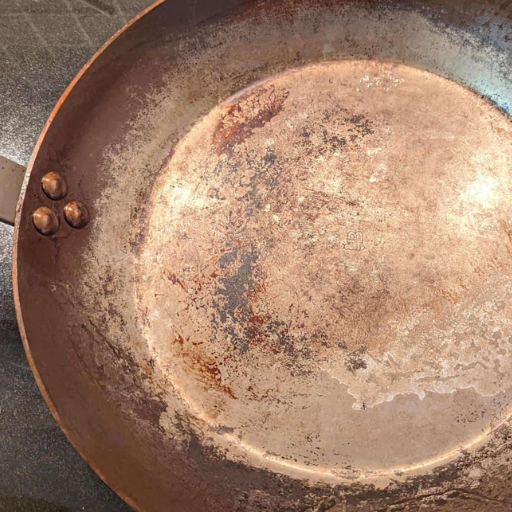
When it comes to preventing carbon steel from rusting, a combination of protective strategies and technological advancements needs to be implemented. Detailed methods follow, with some data to illustrate the effectiveness of these methods:
- Protective Coating
The idea is to paint, epoxy, or powder coat the steel, thus creating a preventive barrier against moisture and oxygen from the environment. For example, epoxy-coated steel could reduce corrosion rates by a staggering 80% in marine conditions.
- Galvanizing
Galvanization is the process of coating carbon steel with zinc for cathodic protection since zinc oxidizes before the steel beneath. It has been reported that galvanized steel can last for 50 years or more in a rural environment, but typically for 20-25 years in an industrial or marine environment.
- Cathodic Protection
Opposing the oxidation of steel surfaces using electrical current or sacrificial anodes (typically zinc or aluminum) is a form of cathodic protection. Available data reveal that cathodic protection significantly reduces corrosion rates, particularly for buried or submerged pipelines.
- Chemical Treatments and Corrosion Inhibitors
Anti-corrosion materials, such as chromates or phosphates, can be applied to steel to form a protective chemical film. Waterborne corrosion inhibitors for steel structures have demonstrated efficacy of up to 90%, particularly in industrial applications.
- Environmental Control
Controlling the environment around the construction, such as maintaining a low humidity level and minimizing pollutants, can also make a difference. Research reveals that a relative humidity level below 60% notably decreases rust formation.
- Advanced Alloys and Surface Treatments
Materials science has progressed enough to give rise to high-performance steel alloys with excellent rust resistance. For instance, the introduction of 12% chromium to steel results in stainless steel, which is much less prone to rust. Moreover, surface treatments such as laser or plasma nitriding can boost the corrosion resistance of carbon steel by 30-50%, as revealed through metallurgical studies.
With the combination of these protective measures, the service life of carbon steel-based articles can be significantly extended, reducing repair and replacement costs and contributing to long-term sustainability in the industrial sector.
Techniques to Prevent Rust from Forming
Galvanization
The galvanization process involves coating carbon steel with zinc to prevent rusting. Zinc acts as a sacrificial anode, protecting steel from corrosion. Studies indicate that galvanized steel may last for 50 years or more, depending on the type of environmental atmosphere. It can last for 25 years in a highly industrial atmosphere. Any other anti-rust layer in the atmosphere rarely offers such longevity.
Application of Protective Coatings
Paints, varnishes, and other protective coatings act as barriers, preventing the moisture or oxygen present in the air from reaching the steel. An epoxy-based coating is typically applied in marine environments, and a corrosion reduction of approximately 85% can be achieved.
Maintenance and Cleaning
Keeping steel surfaces free of dirt, salts, and other contaminants can prevent the buildup of aggressive agents. Studies indicate that regular maintenance can increase the life expectancy of steel structures by 20% on average.
Use of Corrosion-Inhibiting Compounds
Corrosion inhibitors can be applied directly to steel or used in industrial processing to slow down rust formation. They work by lowering oxidation rates and can increase a carbon steel’s lifespan by up to 40%.
Environmental Control
Controlling environmental factors such as humidity and temperature of storage or operation helps curb rust. Use dehumidifiers or keep steel products in climate-controlled environments that limit moisture exposure, a significant force in rust formation.
Importance of Seasoning Carbon Steel
Seasoning carbon steel is essential because it creates a protective layer that prevents rust, thereby enhancing durability. In my view, if properly maintained, seasoned carbon steel will not only resist oxidation but also develop improved performance over time, especially in cookware, where it naturally acquires a non-stick surface. This is a simple practice guaranteed to ensure reliability and longevity.
Best Practices for Cleaning Carbon Steel
Key Point | Details |
---|---|
Avoid Dish Soap | Use minimal or no soap to protect the seasoning. |
Hand Wash Only | Wash with warm water and avoid dishwashers. |
Remove Stuck Food | Boil water in the pan to loosen residue. |
Use Coarse Salt | Scrub with salt and oil for stubborn messes. |
Dry Immediately | Prevent rust by drying thoroughly after washing. |
Apply Oil After Cleaning | Rub a thin layer of oil to maintain seasoning. |
Avoid Abrasive Tools | Use non-scratch pads or wooden utensils to protect the surface. |
Re-season When Needed | Heat oil to restore the nonstick patina if seasoning is damaged. |
Prevent Rust | Store in a dry location and keep it away from moisture. |
Handle Rust | Remove rust with steel wool and re-season the pan. |
Common Applications of Carbon Steel
Key Application | Details |
---|---|
Automotive Components | Used in gears, axles, and structural parts. |
Construction | Structural steel for buildings and bridges. |
Machinery | Components like tools, dies, and machine parts. |
Consumer Appliances | Found in refrigerators, ovens, and washing machines. |
Wiring | Electrical wiring and cables. |
Springs | High-stress applications like suspension systems. |
Industrial Valves | Used in pipelines and fluid control systems. |
Medical Equipment | Parts for medical devices and tools. |
Plastic Injection Molds | Used in manufacturing molds for plastic products. |
Railways | Tracks, wheels, and structural components. |
Usage in Cookware: Carbon Steel Pans
Carbon steel pans are very versatile, well-established, and durable cookware. Here are five notable facts and uses of carbon steel pans for cookware:
- High Heat Tolerance
Carbon steel pans withstand incredibly high temperatures; hence, they are considered significant for searing, frying, and even baking.
- Nonstick Surface With Proper Seasoning
Once suitably seasoned, a carbon steel pan will develop an oily, seasoned nonstick attribute, which is particularly handy for certain foods, such as eggs and fish.
- Light Weight Design
These carbon steel pans tend to be lighter and easier to manipulate compared to cast iron, which, in specific ways, aids in tossing or flipping ingredients.
- Durability for Long-Term Use
These pans are very sturdy, lasting even a lifetime if properly cared for, and can even improve with age and use.
- Versatility Across Cooking Methods
These pans can be used on stovetops, ovens, or open flames, allowing carbon steel pans to become a favorite among professional chefs and work well on their own for the home cook.
Industrial Applications and Their Vulnerabilities
This type of steel finds its most industrial applications due to its strength, durability, and affordability. It is extensively used in the manufacture of tools, machinery, construction materials, pipelines, and automotive components. Carbon steel, due to its strong tensile strength and ability to withstand wear and tear, is widely used in the construction and transportation sectors. For example, carbon steel pipelines are laid to transport crude oil and natural gas, as these steel pipes can sustain high pressure and varying temperatures.
The vulnerabilities of carbon steel need to be addressed by the concerned industries. One major concern is the issue of corrosion, particularly when exposed to moisture or harsh environments. Each year, an estimated $2.5 trillion is spent worldwide on corrosion control across various industries, with a significant portion involving carbon steel infrastructure. Again, although strong, being hard can render it brittle at very low temperatures if not specially treated, which is a significant drawback for applications in cryogenics or Arctic construction.
To counter such limitations, industries are increasingly resorting to modern means for their protection, including anti-corrosion coatings, regular maintenance, and the development of new steel alloys that combine strength with corrosion resistance. By adopting these methods, carbon steel remains a valuable resource in various sectors.
How Rust Impacts Performance and Longevity
Rusting has a significant effect on the performance and longevity of carbon steel components. Structurally, it causes a weakening, followed by expensive repairs and operational inefficiencies in industries if left untreated. Here are five ways rust can affect performance and lifespan negatively:
- Reduced Structural Integrity
Rust causes a slow deterioration of carbon steel, thus weakening its structural integrity. This can ultimately lead to the slow decline of vital components, resulting in cracking, fracturing, or complete failure. For instance, a report found that corroded steel loses at least 50 percent of its load-bearing capacity after ten years if no corrosion protection has been applied.
- Decreased Lifespan
Any operation that supports a high transmission rate between the carbon steel surface and rust can precipitate a decreased lifespan of components. Examples include marine equipment exposed to rust five times as quickly as in dry situations, thus demanding continuous replacement or repair.
- Operational Inefficiencies
Rust issues, such as buildup in pipes that block flow or cause friction reduction in moving parts, lead directly to decreased system efficiency. According to a pipeline study, a loss of approximately 30% of flow capacity was attributed to internal rust deposits.
- Higher Maintenance Costs
Because rust damages necessitate continuous repairs and replacements, it causes increased maintenance cost implications for industries. For example, corrosion control in the oil and gas industries consumes substantial proportions, with some reportedly exceeding $2 billion per year.
- Safety Risks
Steel structure degradation due to rust causes serious safety hazards, including failures and accidents. For example, rust-coated reinforcing steel bars in bridges could cause instability of the entire structure, raising the possibility of collapse.
Understanding and addressing these impacts is crucial for the reliable and secure working life of a carbon steel system. Therefore, active measures should be taken to counteract rust through periodic inspections and the use of advanced protective coatings.
Maintaining Carbon Steel for Longevity
- Inspections
Conduct regular inspections to identify any visual and structural signs that may indicate the early onset of rust, corrosion, or damage. Prompt attention to these will prevent further corrosion.
- Protective Coatings
Apply protective coatings such as paints, epoxies, and other corrosion-resistant finishes to protect carbon steels from moisture and oxygen attacks.
- Environmental Control
When feasible, reduce exposure to severe conditions by controlling humidity and minimizing contact with corrosives.
- Maintenance Procedures
Clean the surfaces to remove dirt, corrosion, and other deposits that can hold moisture. Regular maintenance procedures will help maintain the material’s durability.
- Use of Rust Protectants
Apply rust inhibitors or protective oils in areas prone to oxidation and corrosion.
Hence, observing these practices shall encourage the longevity, safety, and reliability of carbon steel structures.
Tips for Regular Maintenance
- Inspecting Frequently
Conduct visual inspections at least every three months to check for possible rust, cracks, or signs of wear and tear. Early detection can ensure that the problem is addressed before it worsens.
- Clean Thoroughly
Wash the surfaces frequently using a mild detergent and water to remove dirt, salt, and any corrosive substances. Other specific cleaning agents may be used in cases of heavy soiling, provided that they are compatible with carbon steel.
- Apply Protective Coatings
Protective paints, primers, or sealants should be reapplied every one to two years to maintain additional protection against moisture and air exposure.
- Control the Environment
Whenever possible, carbon steel should be stored in a dry area with controlled temperature. Extreme humidity or salty atmospheres should be avoided, as they accelerate corrosion.
- Monitor Usage Loads
Loads and stresses applied to the structure must be continuously assessed to ensure they remain within safe limits. Exceeding limits can lead to fractures or deformities over time.
How to Remove Rust from Carbon Steel
Method | Details |
---|---|
Salt and Oil Scrub | Scrub with coarse salt and neutral oil. |
Baking Soda Paste | Apply paste, scrub gently, rinse thoroughly. |
Vinegar Soak | Soak in vinegar, scrub, rinse, and dry. |
Steel Wool or Scouring Pad | Scrub rust with steel wool or an abrasive pad. |
Lemon and Salt | Sprinkle salt, add lemon juice, and scrub gently. |
Rust Eraser | Use a rust eraser with water for persistent spots. |
Potato Method | Rub with a potato dipped in baking soda or salt. |
WD-40 Soak | Soak in WD-40, scrub with steel wool or brush. |
Preventive Measures | Dry thoroughly, apply oil, and store in a dry place. |
Enhancing Corrosion Resistance in Carbon Steel
In increasing corrosion resistance on carbon steel for longevity and methodology purposes, several practices are generally prepared to protect against corrosion with carbon steel, such as:
- Coating of Protective Plates
The coatings should work as barriers separating the steel surface from moisture and oxygen in the environment, such as epoxy, polyurethane layers, or zinc-based paints. Zinc galvanizing, for instance, can provide a service life of 20-50 years for steel, depending on the environment.
- Use of Corrosion Inhibitors
Corrosion inhibitors, such as phosphate or silicate compounds, can be sprayed or applied to the surface of carbon steel. It has been proven that specific inhibitors can reduce the corrosion rate by as much as 50% in aggressive environments.
- Introduce Alloying Elements
Adding elements such as chromium, nickel, and molybdenum to the steel composition increases oxidation and rust resistance. For instance, stainless steel contains chromium in amounts greater than 10.5%, which produces a passive protective layer, making it considerably less likely to corrode compared to standard carbon steel.
- Cathodic Protection
This method is essentially electrochemical, whereby the sacrificial anode (e.g., magnesium or zinc) corrodes in preference to the steel structure. Such an approach has a 90% applicability in the corrosion mitigation of buried or submerged steel structures.
- Maintenance and Inspection
Regular inspection and maintenance of the carbon steel structure are essential to detect early rust damage and signs of distress. Proactive maintenance, as recommended by the National Association of Corrosion Engineers (NACE), has been found to reduce corrosion costs by over 30%.
- Environmental Control
Reducing the impact of corrosive environments, such as high salinity or high pollution levels, dramatically reduces the likelihood of corrosion. In such coastal or industrial zones, this may involve using dehumidifiers to maintain a relative humidity below 50%, thereby slowing down the rusting process.
With such methods in place, from modern materials to advanced maintenance technology, industries can enhance the durability and serviceability of carbon steel while reducing long-term costs.
References
- ScienceDirect: Study on rust layers of carbon steel, weathering steel, and alloy steel – This article characterizes rust layers and their relationship with atmospheric corrosion.
- ResearchGate: Carbon steel corrosion: a review of key surface properties and characterization methods – A critical review of surface analytical techniques for carbon steel in corrosive environments.
- PubMed Central (PMC): Marine Atmospheric Corrosion of Carbon Steel: A Review – Discusses corrosion products, rust layer characteristics, and corrosion mechanisms in marine environments.
Frequently Asked Questions (FAQ)
What is carbon steel rust?
Carbon steel rust refers to the oxidation process that occurs when carbon steel is exposed to moisture and oxygen over time. This leads to the formation of iron oxide, commonly known as rust, which can degrade the integrity of the metal if not properly managed.
How can I prevent carbon steel from rusting?
To prevent carbon steel from rusting, it is essential to keep it dry and protected from moisture. Applying protective coatings such as paint, oil, or galvanization can create a barrier against corrosion. Regular maintenance and storage in a controlled environment can also significantly reduce the risk of rust formation.
What are the signs of rust on carbon steel?
Signs of rust on carbon steel include a reddish-brown discoloration on the surface, a rough and flaky texture, and the presence of small pits or holes. If you notice these signs, it is important to address the rust promptly to prevent further damage.
Can rust on carbon steel be removed?
Yes, rust on carbon steel can be removed using several methods such as sanding, grinding, or using chemical rust removers. For light rust, a mixture of vinegar and baking soda can be effective. It is important to thoroughly clean and protect the surface after rust removal to prevent recurrence.
Is rust on carbon steel harmful?
Rust on carbon steel can be harmful as it deteriorates the metal and compromises its structural integrity. It can lead to failures in applications where strength and durability are crucial. Therefore, addressing rust issues promptly is essential to maintain safety and functionality.
What is the difference between rust and patina on carbon steel?
Rust is the result of corrosion that causes the deterioration of metal. At the same time, patina is a natural protective layer that forms on the surface of carbon steel, often giving it a desirable appearance. Patina can help protect the metal from further rusting, whereas rust indicates damage that requires attention.
Can I use carbon steel tools in humid environments?
Using carbon steel tools in humid environments requires extra precautions to prevent rust. It is advisable to keep the tools dry, apply protective oils, and store them in a climate-controlled space. Regular cleaning and maintenance are also crucial in mitigating the effects of humidity.
How does temperature affect the rusting of carbon steel?
Temperature plays a significant role in the rusting process of carbon steel. Higher temperatures can accelerate the oxidation process, especially in the presence of moisture. Conversely, cooler temperatures can slow down the rate of rust formation, but humidity levels still need to be monitored to prevent corrosion.