Strength, durability, and corrosion resistance make stainless steel widely used in construction and food processing industries. The 304 stainless steel grade is the most cost-effective and flexible of its many grades. This blog post will delve into understanding the thermal conductivity of 304 stainless steel. Its comprehension is necessary in the design of heat exchangers, industrial equipment, and kitchenware, where heating is a significant factor to consider.
This article aims to summarise thermal conductivity characteristics, analyze how 304 stainless steel compares with other materials, and determine the reasons that affect heat transfer in the material. Readers will understand the performance of 304 stainless steel so thermally efficient designs can be developed for different applications.
What is the Thermal Conductivity of 304 Stainless Steel?
Compared to aluminum and copper, 304 stainless steel has low thermal conductivity grades ranging from 16 to 25 W/m*K. Since 304 stainless steel is not thermally conductive, it can be beneficial when integrating it in systems that need thermal insulation or resistance. In addition, stainless steel is highly corroded and strong, making it a good choice for a variety of applications across many different industries.
Thermal Properties of 304 Stainless Steel
Due to its low thermal conductivity compared to aluminum or copper, stainless steel is less effective at transferring energy when it comes to heating. This, along with its unique strength and resistance, makes it an excellent material to use when prioritizing insulation or thermal resistance.
How Thermal Conductivity of 304 Compares to Other Metals
During thermal conductivity comparisons for 304 stainless steel, the value of 16 to 25 W/m∙K at room temperature is lower than most metals. Consider the following values:
- Aluminum: Its outstanding thermal treatment makes it highly beneficial in varying industries. Its thermal conductivity value is around 205 W/m∙K.
- Copper: Highly recognized as one of the best electrical conductors of heat, copper is worthy of the Bronze f award during thermal conductivity comparisons at 385 W/m∙K.
- Titanium: With a value of around 21.9 W/m∙K, titanium is somewhat closer to stainless steel in conductivity comparison but is still superior.
This case is sufficient to emphasize that 304 stainless steel is not precious to applications that require heat transfer efficiency. Still, its lower thermal conductivity value, along with its mechanical strength and corrosion resistance, makes it useful in applications where heat retention or insulation are key fundamentals, such as cookware, industrial equipment, and architectural features.
Factors Affecting Thermal Conductivity in Austenitic Stainless Steel
Their thermal conductivity should be considered to maximize the impact of austenitic stainless steels in various applications. Following are the critical remarks:
- Composition
The chemical composition of austenitic stainless steel has a predominant influence on its thermal conductivity. Austenitic grades (such as 304 and 316) contain significant amounts of chromium, nickel, and molybdenum, which decreases their thermal conductivity even further compared to the base metals. For example, 304 stainless steel is known to have ~ 16.2 W/m.K of thermal conductivity at room temperature, while 316 stainless steel has slightly lower thermal conductivity, about 13-14 W/m.K.
- Temperature
An increase in temperature also decreases the thermal conductivity of austenitic stainless steel. Thermal conductivity is significantly reduced (above 500°C), which renders ferritic and even martensitic stainless steels ineffective for such applications.
- Microstructure
The face-centered cubic (FCC) crystal structure is fully austenitic and has an inherently lower thermal conductivity than martensitic or ferritic stainless steel microstructures. This is because the lattice structure inherently reduces the conduction of thermal energy.
- Cold Work and Grain Size
Mechanical deformation, also known as cold working, can affect the thermal conductivity of stainless steel due to the effects on its grain structure. Grain refinement often diminishes thermal conductivity since smaller grains hinder heat flow.
- Surface Finish and Coatings
Thermal performance may also be affected by surface coating treatments or the roughness of the surface finish. Depending on the coating materials, thermal conductivity may or may not be inhibited due to coatings implemented for corrosion resistance.
This explains why austenitic stainless steel is selected for its corrosion resistance and mechanical properties but not where high thermal conductivity is needed. Attention to these details is essential when choosing what grade of stainless steel to use in thermal management systems. Always consult material data sheets or a metallurgical specialist for particular engineering applications to confirm adequacy.
How Does 304 Stainless Steel Compare to Other Stainless Steel Types?
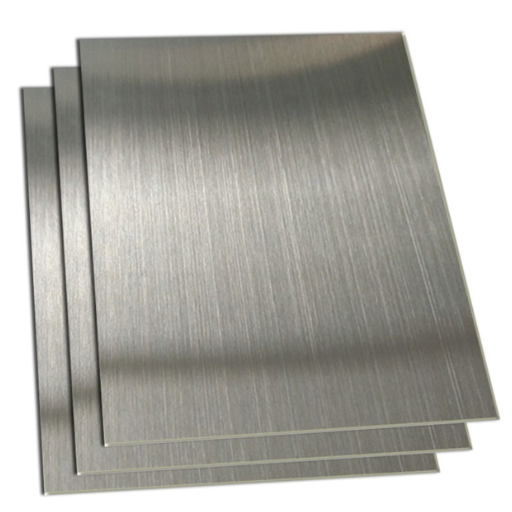
After examining various grades of stainless steel, I have found that 304 grade is most famous for standing against corrosion, especially in mild conditions. Its versatility and affordability make it a preferred choice in general-purpose applications. 304 grade excels in less corrosive environments, while 316 grade, which contains molybdenum and is more resistant to chlorides and marine environments, performs much better than 304 in more corrosive settings. 304-grade stainless steel also withstands harsh welding conditions better than 430-grade stainless steel, which is a ferritic grade and has an austenitic structure, 304 grade is more prone to stress corrosion cracking than duplex grades.
304 vs 316 Stainless Steel Thermal Conductivity
Between 304 and 316 stainless steel, 304 has better thermal conductivity than 316. While both still possess relatively low thermal conductivity compared to other metals such as aluminum or copper, the 304 grade is more efficient in heat transfer processes. However, these differences are so minor that they would not be beneficial in most situations, especially considering 316’s additional corrosion resistance in severe conditions.
Comparing Thermal Conductivities Across Different Stainless Steel Grades
While comparing the thermal conductivities of different grades of stainless steel, it is essential to consider the particular requirements of the task. For the two common grades of stainless steel, 304 and 316, the thermal conductivity ranges from 14 to 16 W/m·K at room temperature. Grade 304 has a thermal conductivity of 16.2 W/m·K, whereas grade 316 possesses a lower thermal conductivity of 14.6 W/m·K. Although there is a difference in those two numbers, in most practical situations where heat transfer is not the headache, those numbers become practically the same.
When compared to aluminum (205 W/m·K) and copper (385 W/m·K) that have much higher thermal conductivity, the use of stainless steel grades is not ideal when heat dissipation is critical. Instead, these grades focus on strength, corrosion resistance, and durability to a greater extent. Thus, with the minimal differences in 304 and 316 thermal performance, the external environment and chemical resistance will likely be more critical. As a result, the strengths and weaknesses of the differing insulations tend to average out. With that said, the insulation performance does not significantly deteriorate.
Why 304 Stainless Steel Has Lower Thermal Conductivity Than Carbon Steel
The lower thermal conductivity of 304 stainless steel compared to carbon steel can be attributed to the slice of chromium and nickel used in its alloying. High amounts of alloying elements come with better strength and corrosion resistance but poorer conductivity. Carbon steel, which is largely made up of iron, has very few alloying elements, so it has better thermal conductivity. The subpar performance of 304 stainless steel is meant to ensure better durability with a bit of thermal performance.
What Applications Benefit from 304 Stainless Steel’s Thermal Properties?
Even though 304 stainless steel has a low thermal conductivity compared to materials such as carbon steel, it is appropriate for use in places where resistance to environmental factors and durability are important. This alloy is often employed in heat exchangers and kitchen appliances, as well as in industrial piping, where moderate thermal performance is required but strength and corrosion resistance are critical. Its ability to withstand varying temperatures without compromising the structure makes it useful in food processing and chemical manufacturing industries, requiring long-lasting, reliable materials.
Food Processing Applications and Thermal Conductivity
Due to its moderate thermal conductivity, excellent durability, and hygienic properties, stainless steel is paramount in food processing. Stain steel’s thermal conductivity is generally within the range of 14–16 W/m·K, which is adequate for achieving uniform heat distribution during cooking and cooling. This property aids in maintaining product quality during pasteurization, sterilization, and baking. In addition, the corrosion resistance of stainless steel protects against contamination from rust, chemical reactions, or any corrosion, retaining food safety and industry standard compliance, such as with the FDA.
For some applications that expect certain resiliency to high or low temperatures, the use of stainless steel grades 304 or 316 is widely accepted in specific environments with temperature ranges of -200 °C to 800 °C. These grades are particularly suitable for acidic or salty food products due to their resistance to chemical attack. In addition, the absence of surface roughness helps reduce the number of microbes on the surface; therefore, stainless steel becomes necessary for food processing environments.
Architecturally Exposed Structural Steel Applications
Architecturally Exposed Structural Steel (AESS) is highly relevant in modern construction, where the structure appeals significantly as part of the overall design. Structural steel AESS is fabricated, finished, and installed precisely to meet structural and aesthetic needs. The most common applications are bridges, stadiums, airports, high-rise buildings, canopies, and a host of other structures, for which the intended design integrates steel construction works without obscuring the building’s beauty.
Essential Features and Parameters of Engineering:
- Design Characteristics:
- AESS components have the most stringent viewing tolerances and fabrication requirements, which include smooth fusion seams, surface treatment depth and uniformity, and low surface irregularities.
- The surface treatments, blast cleaning, and use of specialized coatings vary to eliminate focus and meet esthetics standards.
- Selection of Materials:
- Due to their advantageous mechanical properties and good weldability, structural steel grades of A992, A500, and A572 are commonly used.
- Galvanic and weathering steels (Corten steel) are used for selected environmental conditions due to their protective nature against corrosion.
- Nominal Values:
- Fabrication tolerances are more precise than those given to structural steel so that an orderly appearance is enhanced and parts are aligned. For example, in high-standard cases, alignment tolerances may be set as stringent as +/- 1 mm.
- Standard of Performance:
- The use of high-performance paint systems or power coatings, which form the protective cover, assures a long-lasting, appealing look and protection.
- Steel for polished or satin finish is often used where the exposed interior parts of the structure are intended, improving beauty.
- Requirements for Performance:
- The structure should be able to support the loads within the design limits and be visually appealing.
- The materials are custom-designed for a given region to endure environmental forces like changes in temperature and humidity.
Architecturally Exposed Structural Steel integrates structural efficiency and design creativity, and architects, engineers, and fabricators must coordinate this to obtain optimal design and functionality.
When Low Thermal Conductivity is Advantageous
Markedly low thermal conductivity has its advantage in heat transfer, which must be carefully regarded when building insulation or insulation for structures sensitive to any temperature change. The lesser the thermal conductivity, the easier it is to sustain energy efficiency, which means lesser heat loss in winter and lesser heat gain in summer. In addition, these materials protect structural elements from damage due to excessive and rapid changes in temperature, making it easier to for the occupants to live comfortably.
How Does Chemical Composition Affect 304’s Thermal Conductivity?
The thermal conductivity of 304 stainless steel is affected by its chemical composition. Mainly consisting of iron, chromium, and nickel, the five elements define how heat will be transferred in to the material. Chromium improves corrosion resistance, but its metal has lower thermal conductivity than many others, which decreases the heat transfer rate. Nickel enables the alloy to withstand high temperatures and is also known to make materials weak thermally. Controlled amounts of carbon and manganese form trace components in 304 stainless steel so that they do not change anything but do count. The proportion of these elements ensures that 304 stainless steel will have moderate thermal conductivity. This level will be good for many purposes where there is a need for strong materials, but at the same time, they have to be well managed in terms of the temperatures.
Microstructure of Stainless Steel and Heat Transfer
Every material or component has a specific structure or arrangement, directly affecting its heat transfer features. Basically, with the composition of alloy and heat treatment, the arrangement of the austenite and ferrite phases is set by thermal conductivity. For example, austenitic stainless steels have a lower thermal conductivity than ferritic grades because they possess a face-centered cubic structure. Besides, the thermal conduction also increases because of the reduction in grain size and distribution. Because of all these various reasons, stainless steel is accepted for many applications involving heating because of the phase balance and structural arrangement.
UNS S30400 Specifications and Thermal Properties
UNS S30400, also known as 304 stainless steel, is an austenitic grade of steel that is well-known for its versatility and outstanding corrosion resistance. Its primary features and properties, as well as its elastic and thermal characteristics, are described below.
Chemical Composition (Weight %):
- Chromium (Cr): 18.0 – 20.0%
- Nickel (Ni): 8.0 – 10.5%
- Carbon (C): ≤ 0.08%
- Manganese (Mn): ≤ 2.0%
- Silicon (Si): ≤ 1.0%
- Phosphorus (P): ≤ 0.045%
- Sulfur (S): ≤ 0.03%
- Iron (Fe): Balance
Thermal Properties:
- Thermal Conductivity:
- 16.2 W/m·K at 100°C
- Depending on the conductivity of ferritic stainless steels, the austenitic structure has *** lower thermal conductivity.***
- Specific Heat Capacity:
- 500 J/kg·K at 20°C.
- Coefficient of Thermal Expansion:
- 16.5 × 10⁻⁶ /K between 20°C and 100°C.
- Melting Range:
- ~ 1400°C to 1450°C.
Applications Related to Thermal Properties:
Due to its austenitic structure’s lower thermal conductivity, UNS S30400 is ideal for use in food processing equipment, heat exchangers, and building facades. Its thermal stability and conductivity increase its resistance to thermal stress and the integrity of the structure at varying environmental temperatures.
What Factors Influence the Thermal Conductivity Measurements of 304 Stainless Steel?
Stainless steel, 304 in particular, is significantly affected by other parameters as well, these include the temperature, composition as well as the microstructure of the material. Conductivity is directly affected by temperature, in the case of 304 stainless steel it normally drops with the rise in temperatures. Stainless steel can also be impacted by varying impurities and even the presence of alloying materials, which could be expected to alter heat transfer. Lastly, grain size and phase of distribution determine how effective heat transfer would work depending on the microstructure.
Temperature Effects on Thermal Conductivity
The thermal conductivity of 304 stainless steel decreases with an increase in temperature. This phenomenon occurs because the increased lattice vibrations associated with higher temperatures scatter the heat carriers, reducing heat transfer efficiency. For example, the room temperature thermal conductivity for 304 stainless steel is approximately 25 degrees Celsius (16.2 W/m·K) and reduces to around 14.0 W/m·K at 500 degrees Celsius. Above and beyond 500 degrees Celsius, the thermal conductivity continues to decrease.
Other important technical parameters are:
- The variation of thermal conductivity: 16.2 W/m·K at 25 degrees Celsius to 14.0 W/m·K at 500 degrees Celsius
- The variation of temperature: 25 degrees Celsius up to 500 degrees Celsius or higher as required
- Influence on Composition: The presence of other alloying elements like nickel and chromium will most certainly alter these readings to some extent.
This relationship highlights the problem of overemphasizing temperature-dependent properties when material selection for high temperatures is the focus.
How Annealing Affects Thermal Conductivity of 304
The thermal conductivity of 304 stainless steel is greatly affected by the annealing process’s microstructural changes. The annealing procedure consists of heating the component to a temperature between 1010°C and 1120°C before cooling it quickly. This action relieves stresses internally, helps homogenize the alloy’s microstructure, and may alter thermal conductivity owing to changes in phase composition and grain boundaries.
Some of the more specific aspects of the geometry and annealing parameters, along with 304 stainless steel’s thermal conductivity, are:
- The thermal conductivity post-anneal is isothermally stable at about 16 W/m⋅K near room temperature and is likely more stable throughout a more excellent range of temperatures due to the refined microstructure.
- The reheating range between 1010°C to 1120°C guarantees optimal post-anneal recrystallization and stress relief recovery.
- Mechanical property effect: Higher ductility and lower hardness after annealing would indirectly contribute to enhanced heat removal capability in high-power-density components.
Although annealing processes may cause limited changes in thermal conductivity, they enhance the uniformity and stability of the material under thermal cycling, making 304 stainless steel more useful for materials that undergo different temperature applications.
Measuring Thermal Conductivity Per Meter in 304 Stainless
To obtain the thermal conductivity per meter in 304 stainless steel, I would use the standardized approach of the laser flash method or steady-state measurement techniques. These techniques calculate how well a material conducts heat, and the data retrieved is accurate. Different reputable sources state that the thermal conductivity for 304 stainless steel at room temperature is approximately 16-18 W/m·K. Depending on the other project requirements, the methodology could change, but the measurements for thermal applications need to be accurate to ensure the reliability of the application.
How Does 304 Stainless Steel Compare to Non-Stainless Metals?
304 stainless steels, compared to non-stainless metals, have the most significant advantage due to the combination of corrosion, strength, and maintenance durability. Unlike carbon steel and aluminum, which are common metals, 304 stainless steel does not readily rust or tarnish in the presence of moisture and some chemicals. Although its thermal conductivity is poorer when compared to other metals, like copper or aluminum, which results in lower effectiveness in applications that require heat transfer, the strength, excellent toughness, and long-term reliability compensate for its lower ratings. Such attributes give 304 stainless steel the capability to withstand harsh environments where structural integrity and corrosion resistance are needed.
Stainless Steel vs Aluminum Thermal Conductivity
Stainless steel and aluminum have strikingly dissimilar thermal conductivity, demonstrating superior performance. Aluminum is a superb heat conductor, possessing a thermal conductivity of approximately 205 WS/m·K, which renders it an ideal substance for heat dissipation applications like heat exchangers and radiators. In stark contrast, stainless steel 304 has a thermal conductivity of 16 W/m·K, making it a poor conductor of heat.
These differences emerge effortlessly from the two metals’ different atomic structures and attributes. Due to its lightweight and better conductivity, aluminum effectively dissipates heat, so it is often incorporated in applications requiring high pace heat transfer. While 304 stainless steel may not conduct heat as well, its greater strength, corrosion resistance, and ability to endure harsh environments aid in preserving its structural integrity, making it suitable for applications where thermal conductivity is less critical, but reliability and durability are the priority.
Aluminum is widely used in the production of electronic cooling machines, whereas stainless steel is preferred in industrial and chemical processing equipment where acidic and corrosive substances are present. These materials ultimately depend on what the application requires, which in this case is efficient heat transfer, a certain level of strength, and the material’s ability to withstand hostile environmental conditions.
Comparing 304 Stainless Steel with High Thermal Conductivity Metals
I would first analyze the parameters of the given application when it comes to 304 stainless steel compared to other metals with more favorable thermal conductivity, such as Aluminum or Copper. If the application focuses simply on dissipating heat, then Aluminum and Copper would work best because of their high thermal conductivity. However, 304 stainless steel is advantageous when the application calls for significant corrosion resistance, high strength under stress, and toughness in highly hostile environments. This is why 304 stainless steel is optimal for highly corrosive, high-stress environments where thermal conductivity is unimportant. Balancing the material’s properties with the application’s needs is critical to making such a decision.
Benefits of Stainless Despite Lower Thermal Conductivity
In my view, the advantages presented by stainless steel – especially 304 stainless steel – often supersede its lower thermal conductivity relative to its application. Its superior corrosion resistance allows it to survive in even the most aggressive environment, lowering maintenance and part replacement expenses over time. Furthermore, 304 stainless steel can withstand high stress levels and, therefore, can be used in demanding structural and industrial applications. Although other metals such as copper and aluminum are much better at conducting heat, steel’s strength, low rate of thermal expansion, and ability to endure extreme temperatures without losing its structural integrity make it the best choice for applications where these properties are most important. In the end, stainless steel stands out as the most useful in situations where mechanical durability and resilience are required and not as much efficiency in heat dissipation is needed.
References
- AZoM: Properties of Stainless Steel – Grade 304 (UNS S30400) – A detailed overview of the properties and applications of 304 stainless steel, including thermal conductivity.
- ASM Material Data Sheet: AISI Type 304 Stainless Steel – Comprehensive material data, including thermal conductivity values at various temperatures.
- MetalsCut4U: 304 Vs. 316 Stainless Steel – A comparison of 304 and 316 stainless steel, highlighting differences in thermal conductivity and other properties.
Frequently Asked Questions (FAQ)
Q: What is the thermal conductivity of stainless steel compared to other metals?
A: The thermal conductivity of stainless steel is considerably lower than that of many other metals. For example, 304 stainless steel has a thermal conductivity of approximately 16 W/m·K at room temperature, while pure copper has about 400 W/m·K. This lower conductivity makes stainless steel a relatively poor thermal conductor compared to metals like aluminum, copper, or carbon steel. The reduced ability to conduct heat is due to the alloying elements in stainless steel, particularly chromium and nickel, which enhance corrosion resistance but impede heat transfer.
Q: How do 304 and 316 stainless steel grades differ in thermal properties?
A: While both 304 and 316 are common stainless steel grades, they have slight differences in thermal conductivity. Grade 304 stainless steel has a thermal conductivity of approximately 16 W/m·K, while 316 stainless steel has a slightly lower value at around 14 W/m·K. This difference is primarily due to 316 containing more molybdenum, which enhances corrosion resistance and reduces heat transfer. Both grades share similar material properties otherwise, including comparable tensile strength and heat treatment process responses. Still, they may be chosen for different applications based on their specific thermal and corrosion characteristics.
Q: What are the advantages of stainless steel vs carbon steel in terms of thermal properties?
A: When comparing the thermal conductivity of these materials, carbon steel has a higher thermal conductivity (around 50 W/m·K) than stainless steel (about 16 W/m·K for grade 304). This means carbon steel transfers heat more efficiently. However, stainless steel offers superior corrosion resistance, a better aesthetic appearance, and a longer lifespan in harsh environments. The choice between these materials often depends on whether thermal conductivity or corrosion resistance is more critical for the specific application. In high-temperature environments where both heat transfer and corrosion are concerns, specialized alloys or composite solutions may be recommended. If you need assistance selecting the right material, contact us at SteelPro Group for expert guidance.
Q: How does the low thermal conductivity of stainless steel affect its applications?
A: The low thermal conductivity of stainless steel becomes advantageous in many applications. It makes stainless steel ideal for thermal barriers, insulating containers, and applications where heat retention is desired. For example, stainless steel is commonly used in thermos flasks, cookware handles, and architectural elements where thermal bridging must be minimized. In contrast, its poor thermal conductivity can be a limitation in heat exchangers or applications requiring rapid heat dissipation. Engineers must consider stainless steel’s lower thermal conductivity when designing systems where heat transfer is critical, often requiring greater surface area or alternative design approaches to achieve desired thermal performance.
Q: What material properties of 304 stainless steel affect its thermal conductivity?
A: Several material properties influence 304 stainless steel’s thermal conductivity. The primary factors include its chemical composition (particularly the high chromium content at 18-20% and nickel at 8-10.5%), crystalline structure (austenitic), and manufacturing process. These alloying elements disrupt the metal’s crystalline structure, impeding the movement of electrons and phonons that carry heat energy. Additionally, any cold during manufacturing can affect its thermal conductivity by introducing dislocations and grain boundaries. The tensile strength and hardness of 304 stainless steel correlate inversely with thermal conductivity – as strength increases through work hardening, thermal conductivity typically decreases slightly.
Q: How does temperature affect the thermal conductivity of different stainless steel grades?
A: Temperature significantly impacts the thermal conductivity of stainless steel; for most stainless steel grades, including 304 and 316, thermal conductivity increases with temperature – contrary to what happens with many pure metals. The thermal conductivity is very low at cryogenic temperatures (-150°C and below), while at elevated temperatures (above 500°C), it can increase by 30-50% compared to room temperature values. This temperature-dependent behavior must be considered when designing equipment for extreme temperature environments. Different types of stainless steel show varying rates of conductivity change with temperature, with austenitic grades (like 304) showing more pronounced increases than ferritic or martensitic grades at high temperatures.
Q: What industries benefit from stainless steel’s lower thermal conductivity?
A: Several industries specifically leverage stainless steel’s lower thermal conductivity as an advantage. The food service industry uses it to serve vessels that keep food warm or cold longer. The building and construction sector employs stainless steel in thermal breaks to prevent heat transfer between interior and exterior elements. Cryogenic applications benefit from stainless steel’s ability to minimize heat leakage at extremely low temperatures. The automotive industry uses stainless steel components in exhaust systems to contain heat. Even consumer goods manufacturers utilize this property in appliances where controlling heat distribution is important. In each case, stainless steel also provides additional benefits like corrosion resistance, aesthetic appeal, and durability, making it the preferred material despite alternatives with different thermal properties.
Q: How can the thermal conductivity of stainless steel be improved if required for specific applications?
A: When higher thermal conductivity is needed while maintaining stainless steel’s other benefits, several approaches can be taken. Composite materials, such as copper-cored stainless steel, offer dramatically improved heat transfer while preserving the corrosion-resistant exterior. Surface treatments like nickel plating can enhance thermal transfer at interfaces. Designing thinner stainless steel components or incorporating fins and increased surface area can compensate for the material’s inherently lower conductivity for some applications. In specialized cases, certain ferritic stainless steels with higher iron content and lower nickel/chromium content offer moderately better thermal conductivity than austenitic grades like 304 and 316. The SteelPro Group can assist in selecting or developing optimized materials for applications requiring specific thermal performance.