Stainless steel is an alloy that can be utilized in various sectors and is appreciated for its strength, rust resistance, and appearance. Stainless steel’s thermal conductivity and capacity to conduct heat are unlike that of other widely used metals, such as copper and aluminum. This post will define thermal conductivity, analyze the role of stainless steel in transferring heat, and compare it to other metals. We will also consider the effects of various factors on the thermal conductivity of stainless steel and the consequences for different industries, including construction, manufacturing, and others. This overview is intended for engineers, designers, and anyone interested in understanding how stainless steel conducts heat and the significance of these attributes in real-world contexts.
What is thermal conductivity, and why is it necessary for stainless steel?
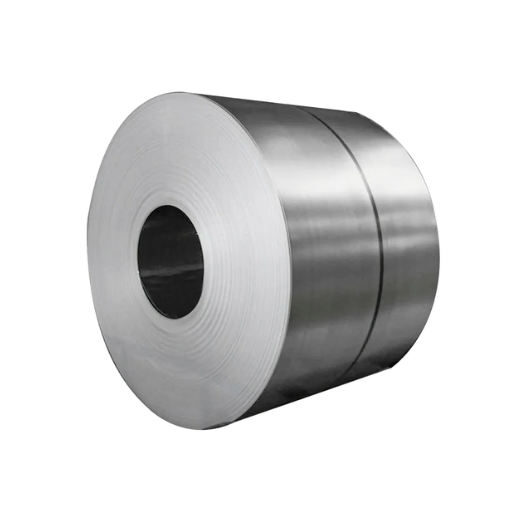
The capability of a material to transmit heat is termed thermal conductivity. Thermal conductivity is an essential trait of stainless steel because it influences how the material performs in cookware, heat exchangers, and industrial machinery, where heat transfer and temperature regulation are critical. Compared to copper and aluminum, stainless steel possesses lower thermal conductivity, but such traits are advantageous in cases where thermal insulation or moderated heating is preferred. This characteristic and other mechanical features further increase suitability in various industries.
Definition of Thermal Conductivity in Metals
Metals with good thermal conductivity possess a significant amount of free electrons. The Thermal conductivity within metals is the material’s ability to transfer heat. Because metals are generally remarkable conductors, the presence of free electrons that move thermal energy is powerful within them. For instance, copper and aluminum are very thermally conductive and are widely used in heat exchangers and electrical wiring. In contrast, stainless steel offers low thermal conductivity, which is beneficial for situations requiring heat to be transferred or insulated from the surroundings. This feature is crucial in picking materials for industrial, residential, and scientific settings where heat performance is considered.
Importance of thermal conductivity in various applications
Effective thermal conductivity is significant in numerous systems because it affects their effectiveness and performance. For instance, copper’s excellent thermal conductivity in electronics helps heat dissipation, which is critical to avoid component failure. In construction, thermal stainless steel or specific composite insulators also aid energy efficiency by controlling heat transfer. Furthermore, having the correct thermal conductivity in heat exchangers and manufacturing equipment improves their efficiency in industrial processes. Choosing the proper material for the desired thermal regulation and system endurance level is vital.
How thermal conductivity affects stainless steel performance
The thermal properties are fundamental to the functioning of stainless steel in its numerous applications. Compared with other metals such as copper and aluminum, the thermal conductivity of stainless steel is significantly lower and can range from 16 to 25 W/m·K depending on the alloy grade and temperature. This means that while stainless steel cannot transfer heat, it is helpful in places where resistance to heat and some level of thermal insulation is needed, such as cookware and heat exchangers. For instance, lower thermal conductivity in industrial applications allows for preserving structural strength at higher temperatures, whereas in cookware, it aids in uniform heating when used with other materials. Meeting the proper grade of stainless steel for thermal performance will depend on the set requirements, such as the range of temperature, the need for heat dissipation, and the mechanical strength of the stainless steel.
How does the thermal conductivity of stainless steel compare to other metals?
Compared to other common metals like aluminum and copper, stainless steel has relatively lower thermal conductivity. Consider aluminum and copper. They are great conductors of heat and, therefore, useful in making heat exchangers and electrical wires. Stainless steels do not conduct heat as well as alloys, but they can resist corrosion, are durable, and are strong in high temperatures. These characteristics help use stainless steel in areas needing heat retention, structural integrity, and environmental factors.
Thermal conductivity of stainless steel vs carbon steel
Compared to carbon steel, the thermal conductivity of stainless steel is much lower. Usually, stainless steel has a thermal conductivity value between 15 and 25 W/m·K, varying with the grade, such as 304 or 316 stainless steel. In contrast, carbon steel has higher thermal conductivity, usually approximately 45 to 60 W/m·K. The difference in thermal conductivity makes carbon steel more suitable for transferring heat efficiently, which is ideal for cookware or heat exchangers. Additionally, the low thermal conductivity of stainless steel lets it retain heat for a more extended period, which can be helpful in controlled environments with certain temperature limits. In choosing between the two materials, the specific thermal needs of the application, along with other considerations such as strength and resistance to corrosion, must be factored in.
Comparing stainless steel to high thermal conductivity metals
When pitted against stainless steel, metals like copper or aluminum with high thermal conductivity are more useful for most applications. For industrial heat exchangers or electronics cooling systems, copper or aluminum are more suitable because they dissipate heat efficiently. On the other hand, stainless steel makes much more sense for specific cookware or insulated containers where heat retention is prized. Furthermore, stainless steel is much more durable and corrosion-resistant, offering value in hostile environments. Considering these variables, I can decide which material is best for each job.
Stainless steel’s position among thermal conductors
Compared to copper, having a thermal conductivity of 400 W/m · K, and aluminum, at 205 W/m · K, stainless steel, which has a thermal conductivity rating of 15-25 W/m · K, is an outlier. While it is not proficient when dealing with applications needing quick heat transfer, stainless steel’s versatility is invaluable in applications with more extreme environments, especially where heat retention is favored. With these parameters in mind, I deem stainless steel an exceptional candidate for long-lasting insulated containers and durable cookware.
What factors influence the thermal conductivity of stainless steel?
The thermal conductivity of stainless steel is influenced by a couple of factors, including alloy composition, temperatures, microstructure, and the specific grade of stainless steel. Overall, higher chromium and nickel content inhibits thermal conductivity and microstructure, including grain size and impurities or defects, which also affects heat transfer. Moreover, temperature impacts thermal conductivity: it usually decreases as the temperature gets lower and increases as the metal heats up. A specific grade of stainless steel also impacts the austenitic grade, which has lower thermal conductivity than the ferritic or martensitic grade.
Effect of Alloying Elements on Thermal Conductivity
Alloying elements affect stainless steel’s thermal conductivity due to the phase transformation of the metal’s microstructure and the impact on electron transport properties. For instance, chromium and nickel tend to lower thermal conductivity in some austenitic stainless steels because of increased electron free-flow scattering. However, aluminum and copper are known to improve thermal conductivity in other grades.
Western Technical Parameters:
- Nickel (Ni): Average of 8-10% in austenitic grades – improves corrosion resistance while further lowering the thermal conductivity
- Molybdenum (Mo): Added in amounts up to 2-3% in higher grades of steel, Mo improves strength at elevated temperatures while only marginally reducing thermal conductivity.
- Carbon (C): Present in tiny amounts 0.02-0.10% – does not significantly impact thermal conductivity in the short term, yet can indirectly influence grain boundary.
- Copper (Cu): Present in some alloys at 1-2% – has the potential to improve thermal conductivity.
- Chromium (Cr): Generally 16-18% with an average in austenitic grades; considerably lowers thermal conductivity due to additional electron scattering.
Understanding the balance of these elements is vital for customizing stainless steel for specified usages where the thermal conductivity and other characteristics are incompatible with the intended purpose.
Impact of temperature on stainless steel’s thermal properties
Stainless steel is broad regarding diverse alloy grades, each applicable to different industry segments. In my opinion, the thermal properties of stainless steel are affected the most by temperature. In my understanding, the thermal conductivity of stainless steel increases as temperature increases, though still lower than metals such as aluminum or copper. On the other hand, the exact behavior depends on the alloy composition; for example, higher chromium and nickel content help retain strength with elevated temperatures. Even with the changes in conductivity, stainless steel boasts its durability and thermal expansion resistance, making it reliable through a broad range of temperatures. Because of this, it is best suited for applications requiring heat resistance and structural stability.
Relationship between electrical and thermal conductivity in stainless steel
The connection of electrical and thermal conductivity in stainless steel is embedded in its physical properties. Styl steel has much lower electrical and thermal conductivity than pure metals like copper or aluminum. This is because it is more resistive due to alloying components like chromium and nickel, which form lattice defects and disrupt the flow of electrons. To put this into context, the majority of stainless steel grades have thermal conductivity values from 15 to 25 W/(m·K) and electrical resistivity ranging from 70 to 100 µΩ·cm. Although there is a correlation between thermal and electrical conductivities in metals, alloying components in stainless steel tend to decrease both properties to some extent, making stainless steel less conductive but more practical for many engineering applications that involve corrosion resistance and structural support.
How do different grades of stainless steel vary in thermal conductivity?
The differences in the grade of stainless steel relate to their composition and internal structures. For example, austenitic stainless steels in the 300 series tend to have lower thermal conductivity than ferritic and martensitic grades because they have more nickel and chromium. Grades 304 and 316 have thermal conductivity values of about 15 W/(m·K), while ferritic grade 430 has thermal conductivity values closer to the above range of 20-25 W/(m·K). Other alloying constituents like manganese and molybdenum also affect these values, and therefore, each grade can cater to different applications based on the required heat transfer.
Thermal conductivity of 304 stainless steel
The thermal conductivity of 304 stainless steel is 15 W/(m·K) at room temperature. Compared to aluminum, it is less thermally conductive, but it is good enough for many industries that require corrosion-resistant and durable materials. Even though the thermal conductivity of stainless steel is relatively low compared to other metals, this is an acceptable cost for the alloy’s excellent strength and oxidation resistance.
316 stainless steel and its thermal conductivity
316 stainless steel is an alloy with a wide scope of applications due to its fantastic corrosion resistance, particularly in chloride environments. The thermal conductivity and resistance properties of 316 stainless steel, slightly over 16 W/(m·K), are better than 304 stainless steel. Compared to 304 stainless steel, 316 stainless steel has the same conductivity but prefers toughness, strength, and resistance to chemical attack. Because of its durability and corrosion resistance, it is also applied to the marine, chemical processing, and medical industries.
Comparing thermal conductivities across stainless steel grades
Heat conductivity for metals such as copper and aluminum is considerably high, resulting in stainless steel being lower in comparison. It is clear that, when comparing stainless steel grades 304 and 316, heat transfer efficiency is sacrificed for durability and corrosion resistance. The same goes for 304 stainless steel, which has a thermal conductivity of approximately 16 W/(m·K) at room temperature, while 316 is equally measured. Even though stainless steel is not ideal for furnaces and stoves due to its weak heat conductivity, its extensive usage in marine, healthcare, and chemical industries is mainly due for toughness, chemical resistance, and strength.
What are the practical implications of stainless steel’s thermal conductivity?
Due to its lower thermal conductivity, stainless steel is not as efficient at transmitting heat as copper or aluminum. This makes it inappropriate for use in rapid cooling processes, such as electronics or heat exchangers. However, it can be useful in situations where it is essential to limit heat transfer, such as in cookware handles or supporting structures that undergo high temperatures. These practical examples demonstrate the selection of materials based on specific application requirements and their implications.
Applications benefiting from low thermal conductivity
- Handles of Cookware
- Plastic and silicone, which are common materials used for handles, have low thermal conductivity, meaning they do not heat extremely. This prevents overheating, ensuring safety during use.
- Silicones and plastics have thermal conductivity values generally between 0.1 to 0.5 W/m·K.
- Insulation Material
- Used in industries for building and refrigeration to improve energy efficiency by minimizing heat transfer.
- Fiberglass and polystyrene will likely have thermal conductivity values lower than 0.04 W/m·K.
- Protective Equipment for High Heat Environments
- Best fit for parts such as heat shields and fireproof clothing to protect from extreme heat.
- For thermal conductivity value, ceramic fibers and similar materials range between 0.02 to 0.1 W/m·K.
- Automotive and aerospace components.
- Incorporated in exhaust systems and engine insulation or thermal barriers to reduce heat transfer and enhance performance.
- Around 0.05 to 0.2 W/m·K is the average thermal conductivity for ceramic coatings.
These examples show how critical these applications are when choosing materials with the desired thermal conductivity to balance functionality and safety.
Use of stainless steel in heat exchangers and processing equipment
Excellent thermal conductivity, corrosion resistance, and durability make stainless steel ideal for the energy, food production, and chemical processing industries in fabricating heat exchangers and processing equipment. Even at increased temperatures, its oxidation and scaling resistance enables dependable performance in high-pressure environments. Moreover, stainless steel’s ease of fabrication and ability to withstand pressure make it possible to utilize this material in various industries. Stainless steel application promotes efficiency, lowers maintenance requirements, and provides durable equipment.
Balancing thermal properties with other material characteristics
Balancing a material’s thermal capabilities with other properties requires a deep understanding of particular application needs. Stainless steel is preferred due to its unmatched thermal conductivity, mechanical strength, and corrosion resistance, especially in extreme conditions. For example, the thermal conductivity of stainless steel grades 304 and 316 is about 14-16 W/m·K, and its oxidation resistance is around 870-925°C depending on the grade, while their tensile strength ranges from 515 MPa (316 grade) to 620 MPa (304 grade).
How is the thermal conductivity of stainless steel measured?
The thermal conductivity of stainless steel is commonly evaluated with either the steady-state or the transient method. The steady-state technique involves the application of constant heat flow through the material. The difference in temperature across the material is measured and used to calculate the conductivity. The transient method includes measuring the time it takes for heat to travel through the sample after applying an energy pulse, such as the laser flash technique. These methods ensure an accurate evaluation of heat transfer characteristics under certain conditions.
Methods for Measuring Thermal Conductivity in Metals
When measuring the thermal conductivity of metals, I typically apply steady-state or transient methods. The steady-state method is simple. Here, a heat source is used and kept in equilibrium, and the found conductivity value is based on the measured temperature gradient. Conversely, I prefer the laser flash methods as they are fast and more advanced. These methods heat the sample with a laser pulse and measure the thermal diffusion rate. These methods are commonly used because they are found to effectively determine the heat transfer properties of metals and yield accurate results.
Units of Measurement: Watts per Kelvin per Meter
Thermal conductivity is listed in watts per kelvin per meter ( W/m·K ). This unit measures how well a material conducts heat, with higher numbers indicating better conductivity. For instance, metals such as copper and silver have very high values of thermal conductivity, approximately 400 W/m·K and 429 W/m·K, respectively, at room temperature, which means they are excellent heat conductors. On the contrary, stainless steel (16 W/m·K ) or glass (~1 W/m·K) have much lower values, which indicates their poor ability to transfer heat.
Some critical technical features that affect measurement include the thickness and uniformity of the sample, as well as the surrounding conditions. For steady-state measurements, accuracy largely depends on establishing constant temperatures in the gradient and eliminating external sources of heat loss. On the other hand, transient methods such as the laser flash technique require meticulous timing and calibration of time intervals along the specific heat capacity of the tested material. These parameters must match the instrument specifications to obtain acceptable results.
Challenges inaccurate thermal conductivity measurement
As I have learned, measuring thermal conductivity accurately comes with challenges. To begin with, the sample’s uniformity and preparation must be done with precision; otherwise, there will be variation in results. External factors, such as changes in temperature or external losses of heat, affect control heating during steady-state measurements, which is crucial. Also, for transient techniques like the laser flash method, there is a need for precise calibration of the devices and proper setting of the material characteristics, such as specific heat capacity. These challenges show the level of error that can arise from a lack of adequate coordination with the testing procedures and instrumentation requirements.
References
- Comparing the Thermal Conductivity of Stainless Steel to Other Metals
- Thermal Activity In Stainless Steel Compared To Other Metals
- Exploring Thermal Conductivity in Stainless Steel
Frequently Asked Questions (FAQ)
Q: How does the thermal conductivity of stainless steel compare to other metals?
A: Stainless steel has a lower thermal conductivity than many other metals and alloys. While pure metals like copper and aluminum have high thermal conductivity, stainless steel conducts heat less efficiently. This makes it useful in applications requiring thermal insulation or reduced heat transfer. The exact thermal conductivity varies depending on the type of stainless steel. Still, it generally ranges from 12-45 W/(m·K) at room temperature, which is significantly lower than copper (401 W/(m·K)) or aluminum (205 W/(m·K)).
Q: What factors affect the thermal conductivity of stainless steel?
A: Several factors influence the thermal conductivity of stainless steel: 1. Composition: Different alloying elements can increase or decrease thermal conductivity. 2. Temperature: Thermal conductivity can change with temperature, often increasing at higher temperatures. 3. Microstructure: The arrangement of atoms and grain boundaries affects heat transfer. 4. Processing: Heat treatment and manufacturing processes can alter the material’s structure and properties. 5. Grade: Different grades of stainless steel have varying thermal conductivities due to their unique compositions.
Q: Is there a relationship between stainless steel’s electrical and thermal conductivity?
A: Yes, there is a correlation between electrical and thermal conductivity in stainless steel, as in most metals. Generally, materials with high electrical conductivity also exhibit high thermal conductivity. This relationship is described by the Wiedemann-Franz law. However, stainless steel has relatively poor electrical conductivity compared to pure metals, corresponding to its lower thermal conductivity. The presence of alloying elements in stainless steel disrupts the electron flow, affecting both electrical and thermal conduction.
Q: Why is stainless steel considered to have poor thermal conductivity compared to other metals?
A: Stainless steel is considered to have poor thermal conductivity compared to other metals due to its complex alloy structure. Adding chromium, nickel, and other elements to iron creates a more disordered atomic structure, which impedes the flow of thermal energy. This disorder scatters phonons (vibrations that carry heat) and free electrons, reducing the material’s ability to conduct heat efficiently. As a result, stainless steel has a lower thermal conductivity than pure metals or more straightforward alloys, making it useful in applications where heat retention or insulation is desired.
Q: How does the thermal conductivity of different steel types vary?
A: The thermal conductivity of steel materials varies significantly depending on the type and grade: 1. Carbon steels generally have higher thermal conductivity than stainless steels. 2. Austenitic stainless steels (e.g., 304, 316) typically have lower thermal conductivity than ferritic or martensitic grades. 3. Duplex stainless steels often have intermediate thermal conductivity values. 4. High-alloy stainless steels usually have the lowest thermal conductivity among steel types. The specific values can range from 12 W/(m·K) for some high-alloy stainless steels to over 50 W/(m·K) for certain carbon steels at room temperature.
Q: In what applications is the low thermal conductivity of stainless steel advantageous?
A: The low thermal conductivity of stainless steel is advantageous in several applications: 1. Thermal insulation in building construction 2. Cookware handles and kitchen appliances to prevent heat transfer to outer surfaces 3. Exhaust systems in automobiles to contain heat 4. Cryogenic storage vessels to minimize heat ingress 5. Heat exchangers where controlled heat transfer is required 6. Architecturally exposed structural steel in buildings to reduce thermal bridging 7. Industrial furnaces and kilns maintain high internal temperatures. These applications benefit from stainless steel’s ability to resist heat flow, improving energy efficiency and safety.
Q: How does temperature affect the thermal conductivity of stainless steel?
A: Temperature significantly impacts the thermal conductivity of stainless steel: 1. At low temperatures, thermal conductivity generally decreases. 2. As temperature increases, thermal conductivity typically rises. 3. The rate of change in thermal conductivity with temperature varies among different grades of stainless steel. 4. Some stainless steels may exhibit non-linear changes in thermal conductivity across wide temperature ranges. 5. At very high temperatures, radiation heat transfer becomes more significant, complicating the overall heat transfer behavior. Understanding these temperature-dependent properties is crucial when designing systems that operate across varying temperature conditions.
Q: Can the thermal conductivity of stainless steel be modified or engineered?
A: While the inherent thermal conductivity of stainless steel is determined by its composition, there are ways to modify or engineer its thermal properties: 1. Alloying: Adding specific elements can alter the thermal conductivity. 2. Heat treatment: Changing the microstructure through heat treatment can affect thermal properties. 3. Surface treatments: Coatings or surface modifications can influence heat transfer at the material’s surface. 4. Composite materials: Combining stainless steel with other materials can create composites with tailored thermal properties. 5. Porosity control: In powder metallurgy, controlling porosity can affect thermal conductivity. These methods allow for some customization of thermal properties for specific applications in the art of custom steel fabrication.